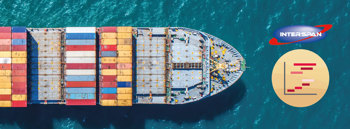
Requirements of the job
With the company set to handle more goods than ever before, the team knew that it's legacy freight forwarding software could not meet all its growing warehousing needs. Instead, it needed a dedicated 3PL warehousing system that would enable it to achieve better stock control, reduce customer invoicing time, maintain high standards of professionalism, and ultimately win new pick and pick contracts.
After finding out more about Access WMS, Interspan’s warehouse managers were confident that the ‘out-the-box’ solution would meet the specific needs of a 3PL as it scaled up operations. Since the software could be rolled out in as little as 7-10 weeks, Interspan Freight could start to streamline its processes and enhance its services, with minimal disruption and downtime. The system went live and was quickly adopted by the whole warehouse team, with improved accuracy and throughput being seen in a matter of days.
Positive outcomes
Interspan Freight has made huge leaps forward in both efficiency and commercial performance in the 12 months since Access WMS went live, and the figures speak for themselves.
On top of an estimated 30% increase in efficiency, the company is now saving around 14 hours a week in admin time. With the software in place, the team no longer has to double-check paperwork because every document is accurate and securely stored centrally. The fact that invoices are automated has made billing customers more accurate, resulting in a revenue uplift of 8%. Interspan Freight also uses the system to better manage peaks and troughs in demand, therefore reducing its reliance on temporary workers.
Even though pick accuracy was always extremely high at Interspan Freight, the process involved a number of stages of human intervention. By automating the process, the company has achieved the gold standard of 100% accuracy faster than ever. Less manual work means operatives are now free to perform other tasks in the warehouse – to the extent that the number of orders completed per day has risen from 300 to 500 with no increase in manpower.
Finally, the software has given Interspan Freight the tools it needs to prove traceability, from when stock is delivered, to the point at which single items are fulfilled. The company can now confidently report on its ability to meet customers’ service level agreements (SLA), ensuring compliance with their standards and OTIF delivery. Delta allows the team to achieve all this because goods are correctly allocated, with no orders taken for out-of-stock items.
As managing director Mark Irwin concludes:
“Access WMS has really improved the way we conduct ourselves as a business – it has helped us increase our revenue and gained us new customers. 3PL is a competitive industry and our customers rely on our 100% pick accuracy and rapid response times. So while our customers win with great service we win with productivity and efficiency gains; a true win-win”
Rob Hodgson, Access WMS specialist commented:
“Interspan have been a pleasure to work with. Their operational team picked up the system within a few hours of training and within a couple of weeks really took ownership. They have been driving the business forward since and I look forward to supporting their growth over the coming years”