What is manufacturing software?
This guide explores different types of manufacturing software and the benefits they can deliver to your business.
Contents
- What is manufacturing software?
- Types of manufacturing software
- Benefits of manufacturing software
- Challenges of using manufacturing software
- Difference between manufacturing software and manufacturing ERP software
- Selecting the right manufacturing software
- The future of manufacturing
- Using Access manufacturing software
What is manufacturing software?
Manufacturing software refers to a range of digital systems that support manufacturing businesses in planning, producing and delivering their products.
These systems automate and streamline core processes, enabling manufacturers to maximise operational efficiency across various functions, gain more control over proprietary data and increase their production speed and capacity.
5 different types of manufacturing software
There are numerous types of manufacturing systems, each designed to underpin certain tasks and processes across the manufacturing production cycle, including:
- Production planning and scheduling – Production planning and scheduling software makes it easy for manufacturers to manage production schedules, plans, capacity and progress. This cuts downtime and ensures every employee, machine and resource is being deployed in the right place and the right time – and to its fullest potential.
- Materials requirements planning (MRP) – MRP software gives businesses full visibility and control over estimates and quotations, purchasing, stock control and production costs. The data gained from an MRP system increases the accuracy of quotations and provides real-time insights on key metrics from quote to invoice, which can inform strategic decisions.
- Stock and inventory management – Inventory management systems save teams countless admin hours by delivering visibility on cash tied up in inventory, whether you’re over or under stocked and ensures you’re ordering at the right time and in the right quantities. This is achieved by automating processes around reordering and stock counts, creating POs and monitoring replenishment levels.
- Demand forecasting – Demand forecasting software allows manufacturing companies to predict demand at different times of the year based on factors including historical data and market trends. Detailed forecasts help to plan capacity requirements ahead of time, while reducing the risk of stockouts or storing surplus inventory for long periods.
- Order fulfilment and shipping – Order fulfilment software is designed to streamline the workflows of 3PLs and both B2B and B2C warehousing operations. They automate time-consuming processes involved with shipping and storage, which helps cut the risk of human error and costly mistakes.
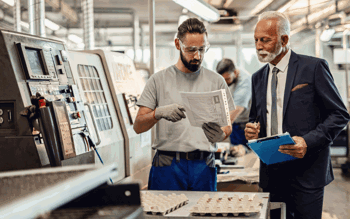
10 benefits of using manufacturing software
- Improved efficiency - Manufacturing software maximises efficiency by providing valuable data insights into performance to focus improvement activities; reducing time-consuming manual processes and supporting clear communication and collaboration enable businesses to cut lead times and deliver more batches at a quicker pace.
- Enhanced stock control - Getting tighter control over stock levels is crucial to maximise productivity and ensure that production is not delayed due to a lack of materials. It also optimises stock levels so that cash tied up in stock is minimised.
- Optimised production planning - Streamlining production planning processes allows manufacturers to create and manage production plans more easily, avoid costly bottlenecks, minimise waste and create a more sustainable manufacturing operation.
- Better quality control - Real-time visibility and traceability across production processes allows for quicker identification and resolution of emerging issues. This is crucial to take proactive approach to reducing defects and ensuring compliance with quality standards and accreditations. Manufacturing software can also help you monitor customer quality and supplier quality as well as internal quality.
- Cost savings - By optimising resource allocation and improving operational efficiency, manufacturers can save on recurring costs such as overtime labour, waste materials and rework.
- Enhanced customer satisfaction - Reducing and providing accurate lead times and optimising quality both of product and service supports client satisfaction and retention.
- Data-driven decision making - Manufacturing leaders can’t just rely on gut feeling to inform key decisions; they should fully utilise the operational data available in the software to spot inefficiencies and opportunities for improvement, using it to direct their core business strategy and key areas of focus.
- Regulatory compliance - Some manufacturing sectors are governed by strict regulations and standards – Good Manufacturing Practice (GMP), for example – which is why having a software to support compliance, safety protocols and completions is a major benefit.
- Scalability - Ambitious manufacturers need agile software that can scale with their business as it grows and evolves, to keep up with greater volumes or greater complexity in production. Paper-based, spreadsheet-based or disjointed systems limit progress.
- Integration - Today’s manufacturing operations involve many moving parts. A centralised platform that seamlessly integrates data and systems is crucial to keep all production functions on the same page and working from a single source of truth.
What are the challenges of using manufacturing software?
Initial implementation costs
Although the initial costs of implementing manufacturing software can pose a challenge, especially for the budgets of smaller businesses, it's important to view the system as a long-term investment in efficiency and growth. Some providers offer a modular system, so you’re not paying for functions that your business doesn’t need – you then have the option to take on more functionality as your business evolves.
Integration complexities
Integrating manufacturing software with your existing tech stack can be tricky, especially if you’re relying on legacy systems which are difficult to connect. Involving IT leaders in the preliminary audit and shortlisting stages is the best way to ensure your platform links seamlessly with other programs and data sources. Some manufacturing software packages, particularly cloud-based ones, bring together MRP, production planning, finance and wider business software (e.g. CRM, HR) into one system. Integrations are already built in and you benefit from streamlining disparate packages with various suppliers to one system with one supplier.
Employee training and resistance
Manufacturers should expect a short-term period of adaptation as teams get used to new software, though this can be minimised by getting internal teams involved in creating the business case and the selection process from the start to gain buy-in; training opportunities, ongoing support and investing in a platform that offers a simple, user-friendly interface also help.
Data security concerns
Every manufacturer should be taking preventative steps to keep company and employee data protected at all times, regardless of their size. Your software should offer robust data protection and encryption features designed to safeguard sensitive information.
Cloud-based software can still cause security concerns in some instances. Working with a supplier with the relevant accreditations such as ISO 27001 is key.
One more thing to consider – the security, back up and disaster recovery features offered by cloud-based manufacturing software providers is very often at a level which many manufacturers can’t match.
Customisation and flexibility limitations
Many software providers offer ‘out of the box’ solutions that can’t be customised to meet specific business needs. Ideally, your software should give your business the ability to plug in additional functionalities as and when needed, so you don’t end up paying for many more features than you’re realistically going to use.
Technical issues and downtime
Manufacturing businesses need to minimise downtime. While switching to a new software may cause temporary disruption as part of the transition process, your provider should mitigate this by helping you plan a smooth launch with minimal impact on production.
Maintenance and updates
Managing updates and patches for security and performance is a standard challenge when maintaining an on-premise manufacturing system for the long term. Rather than seeing it as a negative, these updates are opportunities to benefit from improved features and efficiencies.
Cloud-based manufacturing software removes the need to manage maintenance and updates – one thing to consider when choosing the right solution for your business.
Need for continuous training
Although the learning curve for some manufacturing software can be a challenge, an intuitive, user-friendly platform should reduce the time it takes to get to grips with new ways of working by providing simple tutorials and walkthroughs for employees to follow. Most providers also offer ongoing support and training.
Scalability challenges
Finding a manufacturing software that can adapt alongside the evolving needs of your business is a huge advantage; but not all software providers have the same long-term focus. Make sure to quiz providers on provision for scalability as part of your shortlisting process.
Dependency on technology
The rise of ‘smart industry’ means that manufacturing businesses are becoming increasingly dependent on technology to maximise production and performance – and that reliance will only grow stronger. Manufacturers have no choice but to adapt to new standards and best practices if they wish to remain competitive.
What is the difference between manufacturing software and manufacturing ERP software?
Manufacturing software is a group term that covers any software used by manufacturing businesses to support the various strands of their operations and production cycle.
Manufacturing ERP software is a specific type of manufacturing software solution designed to support enterprise resource planning (ERP) requirements. As far as manufacturing software goes, ERP systems offer a broad range of functionalities designed to meet the needs of engineering, production, operations, sales and finance teams, making them one of the more comprehensive solutions available to manufacturers.
How to select the right manufacturing software for your business
Whether upgrading current systems or digitising processes for the first time, there’s no shortage of choices for manufacturers when it comes to choosing new software to underpin production. Here are a few key tips:
Audit your current system – What specific issues are you having now? What is the business strategy one, three, five years from now? Which systems or integrations are currently in place, and where are they lacking?
Set objectives and budget – Setting objectives is vital in order to benchmark your return on investment further down the line. This should also help pre-empt the costs involved at each stage and determine the scope of your budget.
Involve stakeholders – leaders and teams play a key part of helping businesses scope out a project, support progress and remove bottlenecks, and ensure a smooth implementation.
Research – Searching trusted comparison websites for options and reviews is a good first step, particularly if you are struggling to find recommendations internally or externally. Case studies, message boards and forums are all good places to start.
Compare providers – Most major software providers will be able to offer a free demo so you can get a better idea of how the system can benefit your business. Make sure to factor in criteria such as scalability, ease of implementation, analytics capability, industry specialisation, third party integrations, training and support offerings when comparing systems.
The future of manufacturing?
Technology in manufacturing is evolving at a rapid pace. Rather than replacing humans, today’s systems are freeing up time previously spent on non-value add tasks and empowering businesses to focus more on strategic thinking and people management.
Manufacturing software capabilities are constantly evolving to meet smart industry standards and evolving regulations. That’s why finding a system that can develop over time is such a big advantage. It ensures long-term sustainability, without the need to keep switching systems every two to three years.
Many industrial businesses have already begun to benefit from AI tools, IoT devices and predictive analytics, all of which relies on continuous streams of data to improve accuracy and insight into operations.
Analysing historical and real-time data, machine learning algorithms can predict potential issues and trends, minimising the assumptions built into plans, further supporting operational efficiency.
Remember that decisions made now will impact the success and growth potential of manufacturing companies for years to come – make sure your business is prepared.
Why choose Access manufacturing software?
Access manufacturing software is an end-to-end solution that boosts your bottom line. It's designed to join the dots across your manufacturing operations to give you complete visibility.
- Material requirements planning (MRP)
- Production planning and scheduling
- Business management
- Operations management
- Reporting and analytics
- and more!
Trusted by over 2,000 manufacturing businesses in the UK. See how it could benefit your business today.