Advanced Planning and Scheduling (APS): Everything You Need to Know
Advanced Planning and Scheduling (APS) systems are essential tools in modern manufacturing and supply chain management.
But what is an APS system, and how does it work? APS software optimises production processes by improving resource utilisation, forecasting, and scheduling, all while minimising costs and lead times. Here’s a straightforward guide on the essentials of APS—its key functions, benefits, challenges, and best software options to help your business stay ahead.
Key Takeaways
- APS systems streamline production by optimising resource allocation, reducing lead times, and cutting costs, making them essential for modern manufacturing and supply chain efficiency.
- While they improve real-time visibility and decision-making, implementing APS requires careful setup and employee training to overcome challenges like system complexity and resistance to change.
- Top APS options like Access Orchestrate, Asprova and Simio cater to different production needs, and as APS technology evolves with AI and predictive analytics, it’s becoming even more valuable for businesses aiming to stay agile and competitive.
What is Advanced Planning and Scheduling?
An Advanced Planning and Scheduling (APS) system is a software-driven approach to planning and scheduling that helps manufacturers and supply chain managers make data-driven decisions on production.
Replacing outdated methods like T-cards and whiteboards, APS tools provide real-time visibility into resource availability, capacity, and demand, enabling you to allocate resources efficiently and reduce reliance on manual planning or “gut feel” estimates.
APS System Meaning and Purpose
The purpose of an APS system is to enhance supply chain and production planning by providing insights into resource allocation, lead times, and production constraints. APS systems integrate seamlessly with ERP or MRP software for a comprehensive production management solution. By balancing demand and resource capacity, an APS system helps managers predict material and labour needs and prevent costly downtime.
An APS system is different to an ERP system - find out more about APS vs ERP.
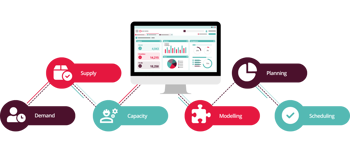
Key Functions of an APS System
APS systems come with core functions that are essential for efficient supply chain management and production optimisation:
Demand forecasting
Using historical data, order patterns, and market trends, demand forecasting helps anticipate stock and resource needs at different times of the year. Tools within APS can also use time series analysis or machine learning to improve forecast accuracy.
Production planning and scheduling
APS software sequences production tasks based on resource constraints and dependencies. By analysing materials, setup times, and lead times, APS systems generate efficient schedules that reduce idle time and maximise output.
Capacity planning
Real-time capacity planning ensures you’re making full use of your equipment, labour, and materials. Continuous visibility into resource status allows you to address issues proactively, avoiding costly delays.
‘What if’ analysis or production modelling
A critical tool within APS, “what-if” analysis lets managers simulate scenarios, helping them prepare for demand changes or supply chain disruptions.
Multi-user functionality
APS allows multiple teams to work from the same live data, making collaboration easy and ensuring everyone operates with a single source of truth.
Advanced Planning and Scheduling Software Brochure
Find out what are the main features of APS software and see how these can help your manufacturing business achieve its goals. Gain an accurate, holistic view of production with Access Orchestrate.
Benefits of Advanced Planning and Scheduling
An APS system isn’t just another tool—it’s a way to streamline operations, reduce costs, and improve production agility. Here’s how APS makes an impact:
Optimised Resource Utilisation
APS helps you make the most of your equipment, labour, and materials, reducing waste and improving cost-efficiency.
Shorter Lead Times
With better-coordinated processes, APS allows you to fulfil orders faster and respond quickly to demand changes, keeping you competitive.
Cost Savings
Reducing operational costs is a key benefit of APS, which minimises labour overtime, resource waste, and inventory costs.
Real-Time Visibility
APS provides up-to-date insights into what’s happening on the production floor, helping managers make informed, proactive decisions.
Enhanced Customer Satisfaction
By reducing lead times and improving delivery reliability, APS contributes directly to better client relationships and loyalty.
Environmental Responsibility
With optimised resource usage, APS supports eco-friendly practices and reduces waste, helping you meet sustainability goals.
Key Challenges in Implementing an APS System
While advanced planning and scheduling tools help improve manufacturing production and management processes, Let’s explore key challenges that manufacturers often face when looking to implement an effective APS system:
System Configuration
APS setup needs to strike a balance: too much complexity makes it hard to maintain, while too little reduces effectiveness.
Resistance to Change
Employees used to manual processes may resist a new system. Clear communication on APS benefits and ROI can help ease the transition.
Regulatory Compliance
In regulated industries, APS must be customised to meet compliance requirements, which may involve extra time and resources.
Training Needs
Staff must be trained on APS software to maximise its effectiveness. Ongoing support is crucial to ensure adoption.
Choosing the Best APS Software
When selecting APS software, one size doesn’t fit all. Consider your company’s unique needs and goals to find the best fit. Here are some popular options:
Software |
Target Audience |
Key Features |
Integration |
Ideal Use Case |
Access Orchestrate |
Small and mid-sized manufacturing businesses |
Real-time visibility, capacity tracking, scenario planning |
Integrates with ERP and MES systems |
Comprehensive production overview with easy integration |
Asprova |
Just-in-time manufacturing environments |
Advanced scheduling, optimises resource usage |
No specific integration noted |
High-demand, fast-paced operations requiring efficient resource management |
Simio |
Companies focusing on risk management |
Simulation capabilities, risk analysis, scenario modelling |
No specific integration noted |
Predicting disruptions and adjusting schedules in dynamic environments |
Monday.com |
General project tracking, not manufacturing-specific |
Flexible project tracking, adaptable for various team needs |
Can integrate with APS and ERP systems |
Teams needing a versatile, customisable project management solution |
“The live plan means different departments can see exactly what is happening. It provides a visual check on jobs to find out how they are progressing and when they are finished. We are also able to carry out accurate ‘what-if?’ scenario planning, so we can provide a completion date for customers and understand the implications of taking on a project.”
How to Implement APS Successfully
Selecting the right APS software is just the start. To implement APS effectively, follow these steps:
- Audit Current Processes
Review your current approach to planning and scheduling to identify inefficiencies and prioritise the features you need most in an APS system.
- Engage Stakeholders
Get buy-in from relevant teams early on to ensure successful implementation and adoption.
- Assess ROI Expectations
Define key performance indicators and make a clear case for APS by identifying the potential impact on production costs, lead times, and customer satisfaction.
The Future of Advanced Planning and Scheduling
APS systems are evolving, incorporating AI, IoT, and predictive analytics to provide continuous data streams that optimise production schedules and improve accuracy. Machine learning algorithms analyse historical and real-time data to identify potential issues, helping manufacturers make smarter decisions faster.
Advanced Planning & Scheduling FAQs
1. What is the difference between ERP and APS software?
ERP (Enterprise Resource Planning) software is designed to manage core business processes like finance, inventory, and human resources across an organisation. It provides a centralised system for tracking data and improving operational efficiency. APS (Advanced Planning and Scheduling) software, on the other hand, focuses specifically on optimising production schedules, managing resources, and balancing supply and demand. While ERP handles overall business operations, APS is specialised for maximising production efficiency and aligning manufacturing processes with business objectives. Read more about the differences on our ERP vs APS software blog.
2. How do I know if I need production scheduling software, or if my current system is sufficient?
If you're finding it difficult to optimise production schedules, manage complex workflows, or handle increasing demand, it might be time to consider specialised production scheduling software. Some signs you may need a more advanced system include frequent delays, high levels of manual intervention in scheduling, difficulty adjusting to changing demand, and limited visibility into real-time production data. A dedicated production scheduling tool can help automate and optimise these processes, improving overall efficiency.
3. Can advanced production and scheduling software integrate with my current systems, like inventory or supply chain management?
Yes, many advanced production and scheduling solutions are built with integration in mind. They are often compatible with existing ERP, CRM, and supply chain management systems, allowing for seamless data sharing and better coordination across departments. When choosing software, look for one that offers robust API integrations or out-of-the-box connectors to your current systems. This ensures that data flows smoothly between platforms and that your team can make more informed, real-time decisions.
Why Choose Access Orchestrate?
Access Orchestrate production planning software enables manufacturers to optimise resource usage across machines, employees, and materials. With real-time tracking and scenario planning, Access Orchestrate helps you manage capacity efficiently and stay flexible, all in one platform.