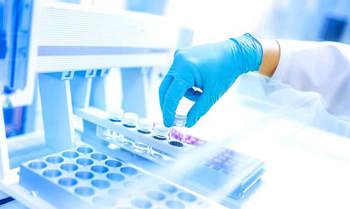
Background
North Carolina is a hub for pharmaceutical and biopharmaceutical innovation and leads the way on vaccine manufacturing.[1] The Research Triangle Region alone is home to nearly 600 life sciences companies, ranging from start-ups to global players.[2]
These enterprises are built on innovation – and, given the investments made in R&D and the challenges they face getting drugs to market, it’s no surprise that growing numbers are looking to optimize their manufacturing processes. They operate in a competitive and regulated industry, where mistakes, inefficiencies and delays are extremely costly.
Better scheduling, using advanced planning and scheduling (APS) software, is a proven way to dramatically increase efficiency, productivity and revenue, particularly in biopharma where processes are inter-dependent and highly-complex.
We began working with a major biopharma company headquartered in North Carolina, which knew its scheduling processes were not as efficient as they could be. This resulted in lost time and missed opportunities to generate additional revenue.
To realize its growth ambitions, the firm swapped manual spreadsheets and whiteboards for automated scheduling using Access Orchestrate – an APS system developed to reduce costs and maximize opportunities with real-time production insights.
As well as integrating with all parts of the business, Orchestrate could deliver web-based dashboards and a dynamic production schedule built on the earliest possible completion time, taking into account complex dependencies and equipment constraints.
A leading and highly-respected university in North Carolina was commissioned to conduct an ROI study on Orchestrate. The software’s success would be judged on three key criteria:
- Transition scheduling from whiteboards to finite capacity scheduling in Orchestrate
- Produce trackable performance metrics within Orchestrate
- Orchestrate to deliver ROI within 24 months.
Requirements of the job
The first task was to understand the pain points the production team faced every day.
One of their biggest barriers to growth was a reliance on multiple whiteboards and documents for scheduling, which did not support collaboration and created a single point of failure. The team was spending several hours a week on manual scheduling and, without access to real-time production data, they found it difficult to adapt or update the schedule.
Shop floor employees also lost valuable time decontaminating every time they left a sterile manufacturing environment to check a whiteboard and when they returned to work again. Another problem was that machine maintenance was not included in the schedule, so machine downtime could potentially cause delays.
Moving from manual to automated scheduling was key to addressing the issues outlined above. Orchestrate would enable the production team to replace their whiteboards and screens with a fully-automated web-based schedule, accessible via any authorized device.
A single live plan, with continuous KPI tracking, would also allow the production team to identify bottlenecks and make process improvements.
Initial findings
Although it is still early days, the researchers came to the following conclusions.
Based on the initial cost for software implementation and maintenance, they estimated that the software would achieve ROI in around three months, well within the projected 24 months.
Importantly, it was found that the team could have produced two more batches per year, resulting in $1m extra revenue if Orchestrate been used last year. Now the site has further capacity to increase the number of batches by nearly 28% on the original figure – opening up a major source of revenue.
All this can be achieved with greater efficiency and improved communication, as detailed below.
Communication
- Changes in the schedule are automatically updated and communicated to the production floor, helping to save time from manual changes and reduce potential wastage.
- Orchestrate automatically creates easy-to-read dashboards for the executive leadership, giving them a better understanding of performance and enabling them to plan more effectively. It also means staff no longer have to trawl spreadsheets looking for information.
Efficiency
- Significantly reduce the time it takes staff to schedule (currently eight hours per week for each employee who undertakes this task), enabling them to put their time to better use elsewhere.
- Eliminates the time employees spend decontaminating to view whiteboards outside a sterile manufacturing environment, then decontaminating again when they return to work.
- Reduces machine downtime, since the calibration maintenance and management system is integrated within the production schedule.
- Supports ‘what-if?’ analysis to find the optimal machine configuration and schedule.
- A further $2.5m could also be saved by rescheduling the cleaning crew to work only day shifts, rather than 24/7 – which would have been near-impossible without the tightly-controlled schedule created in Orchestrate.
Conclusion
There is no doubt that Orchestrate is a game-changer for this company, which was previously missing out on valuable revenue-making and cost-saving opportunities. It was a catalyst for improved working practices that has put it on track to generate the $3.5m identified by the university experts. Finally, it is worth mentioning that the system was live within six months from the start of the project, meaning its time-to-value was extremely short.
Find out more on Access Orchestrate, an advanced planning and scheduling tool.
[1] Source: www.researchtriangle.org/industries/life-sciences
[2] Source: Ibid