Five steps to scalability in manufacturing
As we take stock of the past year, many manufacturers will be thinking about how they can diversify, take advantage of unexpected opportunities and scale up sustainably.
Covid-19 accelerated the pace and scale at which firms were able to roll out new products and enter new markets (the vaccine and Ventilator Challenge being prime examples). As the race to deliver ventilators for the NHS got underway, for instance, we heard some impressive stories of teams collaborating, sharing data, automating processes and repurposing machinery.
There is no question that innovation will be the driving force for growth as the UK emerges from the pandemic and navigates the aftermath of Brexit. Building a solid foundation for growth demands strategic investment in people, machinery and technology, with firms ensuring they’re getting the most from new and existing resources.
Operating at a small-scale, it’s easy to miss inefficiencies that hamper productivity or accept them as the norm. Unplanned machine downtime, under-utilisation of resources, cash held up in inventory, poor on-time, in-full (OTIF) performance and an over-reliance on over-time are all common but costly issues. And unless they get on top of them, firms are unlikely to grow successfully, especially in an uncertain market.
It may only be a matter of time before they experience cashflow problems and struggle to take on and fulfil new customer contracts – damaging their growth ambitions, profits and reputation. Manufacturing management software can help in a number of ways, as outlined below:
Iron out production planning and scheduling issues
Many manufacturers, even bigger ones, rely on spreadsheets to create production schedules but they can quickly run into trouble when they take on new orders. A rigid plan makes it difficult to spot potential problems quickly, like bottlenecks, delays and inefficiencies, and take appropriate action. This is why production managers are increasingly moving towards dynamic or live planning – using real-time data to continually improve the schedule and automatically communicate updates to the team. By making the process more efficient, you can be confident that customer orders will be fulfilled on time.
Understand capacity
Taking on new orders without a clear understanding of capacity is a risky move; you could either end up with bottlenecks and staff working overtime, or people and machines standing idle. A live plan provides complete visibility of staffing and machines, so you’ll identify areas of over and under-utilisation. When a new contract is on the cards, smart modelling tools also help you to understand future capacity based on your constraints.
Perform detailed ‘what-if?’ analysis
Linked to the above, production planning software makes it easy to evaluate a range of work schedule options and create a plan that utilises all resources for maximum efficiency and productivity. When agreeing an order, you can quickly see whether it’s achievable within the customer’s timeframe.
Capture and act on real-time data
Manual reporting methods mean that you don’t always uncover long-standing inefficiencies until it’s too late. By capturing live data during the production cycle, using a handheld or mobile barcode scanner integrated to Shop Floor Data Capture, information is no longer double-keyed (saving time and reducing error). The true cost of production including downtime, wastage or rejected items also becomes clear, paving the way for process improvements.
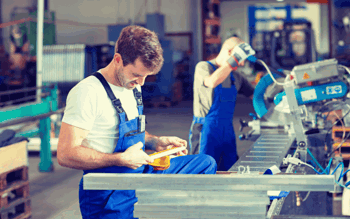
Automate labour-intensive processes
As well as providing automatic schedule updates, your manufacturing management software can also automate many of the time-consuming and error-prone tasks that hamper growth. Material Requirements Planning (MRP) software allows you to automate purchase orders (POs) for materials and components, and work to Just-in-Time (JIT), helping to avoid shortages and reduce inventory costs. Meanwhile, automating invoices prompts customers to pay on time, which improves cashflow.
Automation enables you to achieve economies of scale too, since the system can handle more POs, invoices and evermore complex schedules as the business grows, without increasing staffing costs.
Growing, diversifying or adapting your business model for new market conditions can be risky, which is why every decision should be based on up-to-date and reliable data. Continuous feedback, delivered via a central platform, helps teams to make accurate forecasts and focus their efforts on winning and retaining high-value contracts by exceeding customer expectations.
Find out more about our solutions for manufacturers. You can also find more resources on our manufacturing hub.