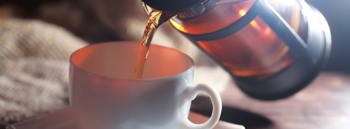
Starting point
Ringtons has been a user of Access software for over 10 years, largely utilising its financial functionality but employing a multitude of other systems to manage the manufacturing and supply chain side of the business. When the company’s IT manager left this began to change.
“We had been very dependent on our IT manager,” explained executive Chairman Nigel Smith.
“And while he was very skilful at his job, I didn’t want such a concentration of knowledge in one person’s hands again.”
The decision was made to outsource IT support and develop a broader base of IT skills within the business. Meanwhile, Nigel commissioned a review of the existing IT systems to decide how to create the comprehensive IT backbone the company would need in years to come.
“The report came back that Access was a very good supply chain system but that we weren’t utilising it very well,” he said.
The company began by upgrading to Access ERP, to create a springboard for integration throughout the company.
“Our focus since then has been to expand the use of Access ERP into all areas,” he continued.
Stock control
The production division had been operating with a variety of IT systems. The location and movement of stock across the two warehouses and manufacturing site were controlled by various spreadsheets, each independent of each other.
“The system was manual, cumbersome and inefficient, and took a lot of man-hours to control and reconcile,” explained head of warehouse and production, Dave Clark.
"We now have a single warehouse system that is accurate, virtually live, and gives us complete traceability."
Before any significant rollout of Supply Chain functionality could take place, stock visibility and control had to be improved. The solution Ringtons chose was to implement Access ERP’s Warehouse Management functionality and introduce handheld devices in the warehouse.
“This has made a big impact,” Clark said.
“We now have a single system that is accurate, virtually live, and gives us complete traceability.”
Materials are barcoded as they come on site. Stock movements are recorded and controlled by barcode scanning. Laborious manual spreadsheet updating has been abolished, reducing the workload for all staff, particularly for supervisors who are now liberated to concentrate on their primary role.
MRP and beyond
Work has already begun on implementing the system’s MRP functionality. Planning and materials requirements are currently managed by two enormous spreadsheets that detail activity for 13 weeks and cover around 400 skus.
“I want to get rid of these,” Clark said. “But we can only do this step-by-step. We had to get our stock control right first.”
Currently, retail sales transactions are held in a standalone system. Similarly, tea stock data, from tea purchase and blending through to packing, is held on a specialist system.
“This is an important system for our business because it’s about the quality of the teas we buy and how we blend them. This differentiates us from our competitors,” Nigel said.
“For us to operate seamlessly, it would be better for all tea stock and all customer transactions to be brought within Access ERP, and we’re currently evaluating whether this is possible.”
Finance
The financial side of the business is also rolling out further functionality. Office Integration is a tool that head of finance David Brown particularly likes.
“I’ve worked in companies with different software, but this is fantastic. I use it for anything from producing management accounts through to ad hoc queries. I simply enter a formula into an Excel spreadsheet, and it draws the data directly from the system. Each time I open the spreadsheet it refreshes the data immediately.”
Every Monday morning, the department runs an Outstanding Debtors report which details all the customers that have reached their credit limit. This is now accessed and actioned through a single Excel spreadsheet.
“We enter either a 0 or 1 against each outstanding debtor to indicate whether to stop further orders on not,” Brown said.
“When we’ve finished we press update, and the system changes the status in Access ERP. It’s a huge improvement on the old method where we had to go manually into each customer’s account then through several screens just to change a single status. It takes half an hour rather than half a day.”
Innovation
The company has been exploring innovative ways of utilising Access ERP. For example, one section of the business supplies tea to a large number of small cafes and shops. The Ringtons bill is just one of many these customers pay every month, and arranging to do this by direct debit would save them time and money. For participating customers, Ringtons runs a report in Access ERP and imports it into a third-party BACs system which collects the money automatically.
“It’s early days yet, but it saves us chasing debts, saves our customers the hassle of raising cheques, and in the long-term we believe it will reduce bad debts.”
Further improvement
Access ERP has been updated again. And from the beginning of the new financial year statements will be automatically emailed out, reducing administrative costs and postage. At the same time, the company will go live with the fixed asset register module, bringing all the information together into a single system to provide instant visibility of company assets and depreciation, saving
time and improving accuracy.
“Our aim,” Nigel concluded, “is to develop seamless integration across the business and migrate from a multisystem business to one strong system with perhaps one or two secondary systems supporting it.”
And the benefits are likely to continue rolling in as this is achieved.