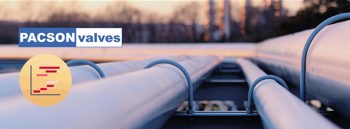
BACKGROUND
Pacson Valves is a Dundee-based manufacturer of bespoke, high integrity valves for the oil and gas industry, employing 86 employees.
When the company began trading in 1992, its products included small bore, high-pressure valves. Since then, and following successful expansion, the range has grown to include more valve types and pressures.
In 2008, Pacson Valves moved from its original premises in Carnoustie, on the east coast of Scotland, to a modern factory at Claverhouse Industrial Park that offered better access to Aberdeen and Edinburgh. Today, it supplies valves to firms working on time and mission-critical projects around the world.
As the company grew, and operations become more complex, managers recognised the need for streamlined production planning and scheduling processes. In what was later dubbed a ‘Year of On Time Delivery (OTD)’, the senior team made improving OTD performance a strategic business goal – something that could only be realised with the right digital platform in place.
REQUIREMENTS OF THE JOB
Pacson Valves wanted to invest in systems, technology and equipment in order to upgrade its operations, and improve reliability and efficiency, while also reducing costs.
Embarking on a strategy to boost OTD performance, the team was determined to improve visibility and move away from manual processes – which included a physical planning board in the machine shop and manual planning of test and assembly operations.
Any digital replacement would also need to integrate with its existing ERP system to improve information flow through the business, laying the foundations for future improvements.
IMPRESSIVE RESULTS
Pacson invested in Access Orchestrate Planning and Scheduling software from Access Group.
Since it was implemented, Access Orchestrate has enabled day-to-day scheduling, capacity, what-if and scenario planning. The outdated planning board has been replaced with an online drag-and-drop Gantt chart which, due to its intuitive design, has been quickly adopted by the Pacson team.
With this software in place and a concerted effort from the whole workforce, Pacson transformed OTD performance from an unpredictable 50%, to a reliable 90%.
More than 95% of orders are now delivered within one week, and with a continuous and detailed review of any missed deadlines, performance continues to improve. Explaining further, Commercial Director John McLaren said:
“The new software has enabled us to remove various manual processes, including our planning board, which used to be at the heart of our operation. Orchestrate has enhanced our ability to anticipate and adapt and as a result we’ve seen a marked improvement in our delivery performance. Operating in the oil and gas sector, reliability and trust in our systems is essential – Orchestrate delivers the confidence our customers need.”
Improved production scheduling means it is possible for businesses like Pacson Valves to improve forecasting and identify potential roadblocks and bottlenecks. As a result, firms can plan how to deploy resources more effectively, to ensure greater efficiency and productivity gains.
Rod Schregardus, a supply chain technology specialist at Access Group, said:
“Orchestrate is designed to be a catalyst for productivity – helping ambitious companies like Pacson Valves to improve visibility, automate manual process and ultimately deliver the best service to its customers. It’s great to see such a significant boost to On-Time Delivery performance following the deployment – something that makes the business case clear and a quick return-on-investment likely.”
NEXT STEPS
Following the success of the project, Access Orchestrate has since been deployed across other areas of the business including engineering, quality and inspection, testing and assembly.
Flexible and easy to use, Orchestrate has been developed for manufacturers like Pacson Valves, where removing manual processes brings measurable commercial benefits. It can be integrated with other systems and its drag-and-drop Gantt Chart functions give users real-time updates on scheduling that enables them to respond rapidly to change.
As well as day-to-day scheduling the software also enables capacity and ‘what if’ scenario planning, to make informed comparisons to evaluate alternative options and make better informed decisions quickly.