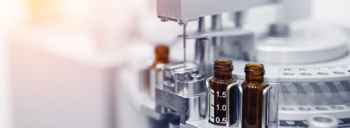
Boosting capacity
The production team responsible for a group of self-medicating products within the plant were faced with the challenge of increasing manufacturing productivity. Access Orchestrate proved to be an ideal tool because, in its day-to-day scheduling role it had automated and built-in all the deep practical expertise of schedulers who understand the plant, the way product moves through it, and the complex conflicts that exist with shared equipment and sequencing.
A company director explains:
“Having put all the process basics into Access Orchestrate, we were able to extend it to become a modelling tool capable of exploring ways to optimise the use of the facility. We were able to identify bottlenecks, to plug in fixes and build ‘what if’ scenarios in a true modelling sense. We then embarked on carefully chosen projects in which we already felt a high level of confidence using Access Orchestrate in a day-to-day scheduling role. We knew they would work.”
“We have just completed a twelve-month programme, removing bottlenecks and optimising the plant and have achieved a 20% faster throughput. We now have higher capacity using exactly
the same resources. That would have been impossible using traditional spreadsheet-type planning and scheduling tools.”
Manufacturing rationalisation
Like so many pharmaceutical companies, this multinational is seeking to consolidate manufacturing into a smaller number of plants. The vaccine in question has a number of sub-types, currently manufactured within different sites in different continents. The plan is to concentrate production within one site.
It has not been possible to accommodate the sub-types within existing facilities, which has meant completely rebuilding and recommissioning an existing suite, resulting in two separate suites.
The company has used Access Orchestrate to secure an understanding of how things will look day-to-day in terms of activities and in terms of resourcing. A future snapshot, as well as a capacity and resource plan. They have been able to model requirements for the next five years, as well as visualising the mix of products to arrive at a realistic plan of action.
The director responsible has extensive experience of such projects and comments:
“Traditionally, spreadsheets such as Excel have been used to plan such activities, typically using a common server to provide an element of shared functionality. The difficulty with such an approach is that it is limited essentially to a chart comprising coloured squares.”
"Access Orchestrate has provided a wealth of information behind that. It’s possible to drill down to hours, minutes, seconds, rather than being restricted to crude day or half day blocks. Equally
important, we have been able to apply ‘what if’ scenarios, particularly around capacity related numbers. It is in the nature of forecasting that the further you move into the future, the less
valid the numbers become.
With Access Orchestrate, we have been able to look at what the forecasters have been saying, and then apply a range of variations. Using spreadsheets it would take days to accommodate secondary or parallel processes, figuring what a schedule might look like, while another team is separately figuring our recruitment needs – everyone speculating from their own spreadsheets. Orchestrate has given us the clarity of vision we need."
Conclusion
The company has been able to use Access Orchestrate’s modelling capabilities in two projects, each with multi-million dollar implications. All that from the same easy to use software they are using for their daily scheduling.