How Much Does An ERP System Cost? A Guide for Construction Professionals
There is a significant variety in the cost of ERP systems depending on a range of factors such as the size and number of users on the system, the platform on which it is hosted, and internal IT resources, among others.
In this article, we will explore the various factors that influence the cost of ERP systems, including construction erp software providing you with the insights needed to make the best decision for your construction business.
Article summary:
ERP systems streamline business processes for construction companies, but their cost varies. Factors include system size, user count, hosting and IT resources.
Perpetual licenses offer customisation but require high upfront costs. SaaS subscriptions are cheaper initially but have ongoing fees. Open-source options are free but require IT expertise.
Beyond the base cost, consider ongoing expenses like training and maintenance. Implementation involves data migration and customisation, and complexity can affect cost. The return on investment (ROI) is complex but can be assessed by looking at factors like productivity gains, cost savings, and fewer errors.
By considering these factors, construction professionals can make informed decisions about construction ERP software.
Answering the question of ‘How Much Does an ERP System Cost’ isn't a one-size-fits-all answer; instead, it involves a nuanced interplay of factors that vary across vendors and businesses.
In the construction industry, where digital transformation is becoming increasingly pivotal, understanding these factors is crucial for making informed decisions that align with your budget, scalability needs, and long-term goals.
By delving into these elements, businesses can better navigate the complexities of ERP investments and harness their full potential to enhance efficiency, productivity, and competitiveness in the construction sector.
What is an ERP System?
An Enterprise Resource Planning (ERP) system is an integrated software solution designed to manage and streamline various business processes across an organisation.
Unlike standalone applications that handle specific functions, an ERP system consolidates multiple functions into a single, cohesive platform. This includes everything from finance, human resources, and supply chain management to project management, procurement, and customer relationship management.
The comprehensive nature of ERP systems means they offer a centralised view of operations, facilitating better decision-making, improved efficiency, and enhanced collaboration across departments.
However, this integration and functionality come with a level of complexity and scale that surpasses most other software solutions. Consequently, ERP systems typically entail higher costs due to the extensive customisation, implementation, and ongoing maintenance required to tailor them to a business's specific needs.
For more information on ERP systems in construction, check out our full article here: What Is Construction ERP?
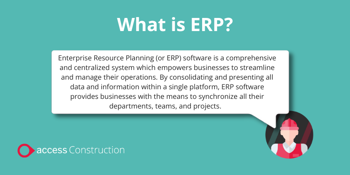
ERP Pricing Models
Various pricing models exist for ERP systems, each offering unique advantages and trade-offs.
Understanding these models is essential for choosing the right ERP solution that fits your construction business's needs and budget.
Perpetual Licensing Models
Leading software providers often adopt a modular costing system, where tailored bundles are crafted after discovery calls to ascertain the specific features a business requires.
These bundles, sold on a per-user basis in the form of licenses, can include a range of functionalities crucial to construction management.
The number of users significantly influences costs, with a proportional increase as more licenses are required. Additionally, companies may opt for additional add-ons, such as CRM integration or supplementary apps at a later stage to enhance their software's capabilities.
Pros:
- Long-Term Ownership: Once purchased, the software can be used indefinitely without recurring subscription fees.
- Customisation: Higher potential for extensive customisation to meet specific business needs.
- Control: Greater control over the software and its deployment.
Cons:
- High Initial Cost: Significant upfront investment required, which can be a barrier for smaller businesses.
- Maintenance Costs: Ongoing costs for updates, support, and maintenance are often the responsibility of the buyer.
- Scalability: Scaling up can be expensive as new licenses must be purchased for additional users.
SaaS Subscription Models
SaaS (Software as a Service) subscription models involve paying a recurring fee, typically monthly or annually, for access to the ERP system. This model is often referred to as an ‘out of the box’ ERP, providing standard functionalities that can be accessed via the cloud.
Pros:
- Lower Initial Cost: Lower upfront costs make it more accessible for businesses of all sizes.
- Automatic Updates: Regular updates and improvements are included in the subscription.
- Scalability: Easy to scale up or down based on the number of users and changing business needs.
Cons:
- Recurring Fees: Continuous subscription fees can add up over time, potentially becoming costly in the long run.
- Less Customisation: Limited customisation options compared to perpetual licensing models.
- Dependency on Provider: Reliance on the service provider for uptime, support, and security.
Open Source ERP Models
Open-source ERP models provide the software’s source code for free, allowing businesses to modify and customise the system extensively. However, this model requires substantial IT resources and expertise to implement and maintain.
Pros:
- Complete Control: Full access to the source code allows for extensive customisation and control over the software.
- Cost Savings: No licensing fees, which can reduce costs significantly.
- Community Support: Access to a community of developers for support and enhancements.
Cons:
- High IT Resource Requirement: Requires significant, highly skilled IT resources for implementation, customisation, and maintenance.
- Complexity: Can be complex to set up and manage, potentially leading to higher indirect costs.
- Limited Professional Support: May lack the professional support services that come with commercial ERP solutions.
Key Factors Influencing ERP Price
The final price quoted for an ERP system can vary significantly due to several factors, making it impossible to state an exact price range. However, below is an overview of the most common factors that affect the cost of ERP systems. Understanding these factors can you and your stakeholders anticipate projected costs and make more informed decisions.
Factor |
Description |
Number of Users |
Costs will increase with the number of users, as more licenses or subscriptions are required. Each additional will usually incur extra fees, with some ERP being sold on a per-seat basis. |
Deployment Method |
Choosing between a on-premises or cloud-hosted ERP system will play an important part in the final price of your solution. The most popular option today, cloud-based hosting provides lower initial costs at the cost of an ongoing subscription fee. Alternatively, on-premises systems require a higher upfront investment for hardware and software. |
Customisation |
Tailoring your ERP system to meet the specific needs of your business can significantly affect costs. For larger companies requiring bespoke implementations, the extensive customisation may require additional development time and resources. |
Implementation |
The complexity and duration of the implementation process can affect costs. Factors include data migration, system integration, and project management efforts and training to ensure your teams can operate the ERP effectively. |
Training |
Specialised training for employees ensures you are getting the most of your new ERP system. However, this will add to the overall cost with some training programs varying in length and complexity. |
Additional Modules and Updates |
Most ERP systems today are sold through a number of packages that include essential modules and features. However, some providers also have a portfolio of additional modules that can be sold on a case-per-case basis. Additionally, depending on your provider, regular updates designed to enhance the functionality of the ERP system may come at an additional cost. |
Want to know more about hosting options for your ERP system? Read our article On-Premise vs Cloud – Which is the Best Way to Host ERP Software?
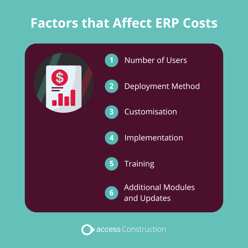
Ongoing ERP Costs to Consider
While base subscription costs constitute a significant portion of the ongoing expenses of an ERP system, businesses must also consider additional costs related to implementation and continuous support.
Ensuring your team and stakeholders are prepared for the long-term investment needed to maintain and optimise a comprehensive ERP system is crucial.
Understanding these common ancillary costs enables more accurate budgetary planning and helps businesses conduct a thorough assessment of the overall financial impact.
Factor |
Description |
Hosting |
Depending on whether your ERP system is cloud-based or on-premise, the ongoing costs can vary. On-premises solutions require continued maintenance of physical servers and infrastructure, meaning updates need to be done manually in some cases. Meanwhile cloud-hosted systems involve an ongoing subscription but move the responsibility of hosting to an external partner, making them increasingly popular choice. |
Staff Training |
Continuous training is essential to ensure employees can effectively use the ERP system. It’s important that you allocate adequate resources for comprehensive staff training to ensure a smooth transition and maximise user proficiency with the new ERP system. Regular training sessions, onboarding for new hires, and updates on new features contribute to ongoing costs. |
Consultancy |
Hiring external consultants for system optimisation, customisation, and troubleshooting can add to the overall expenses. Consultants bring expertise that can be crucial for maximising the ERP system's value but do come at a considerable cost, so always consider this factor into your projections. |
Maintenance and Support |
Regular maintenance, updates, and technical support are vital for the smooth operation of the ERP system. This includes software updates, bug fixes, and 24/7 support services to address any issues that arise. Whilst the cost of these varies from software to software, it is an additional cost-factor you should prepare for early. |
Want to learn more about choosing the best Construction Management Software for your business? Read our Buyer’s Guide to Construction Management Software, which includes a step-by-step checklist.
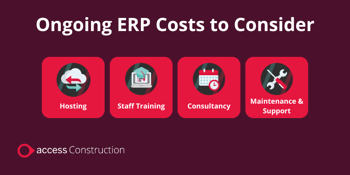
How Much Does It Cost to Implement an ERP System?
Implementing an ERP system is a substantial investment in both time and resources. The process requires careful planning and execution, often involving significant manhours and coordination across multiple departments.
Understanding the key components of the implementation process and their associated costs is crucial for budgetary planning and ensuring a smooth transition.
Initial Implementation Costs:
Perhaps the biggest cost upfront, you’ll need to budget for the implementation, covering essential components such as data migration, customisation, and project management.
Each of these elements is critical for tailoring the ERP system to your specific business needs and ensuring all existing data is accurately transferred and integrated.
Complexity and Size of Business:
Recognize that the complexity and size of your construction business can influence both the time and cost required for effective implementation.
Larger businesses or those with intricate processes may require more extensive customisation and longer implementation timelines, increasing overall costs.
Staff Overtime During Implementation:
Acknowledge the potential need for staff overtime during the implementation phase, particularly for tasks that require additional time or resources.
Employees might need to work extra hours to manage data migration, test new functionalities, and ensure a seamless transition to the new system.
Temporary Increase in Labour Costs:
Factor in any temporary increase in labour costs to manage the workload associated with adapting to the new system. This includes not only overtime pay but also potential temporary hires or contractors brought in to assist with the transition.
Ensuring that you adequately allocate resources and support during this critical phase can significantly impact the success and efficiency of the ERP system once fully operational.
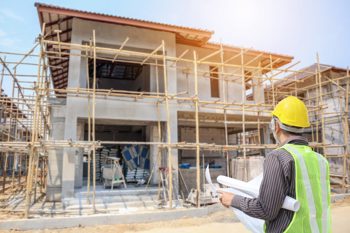
How Do I Determine the ROI of an ERP System?
Calculating the return on investment (ROI) of an ERP system can be complex due to its multifaceted impact on business operations. However, a structured approach can help assess the value generated by the system compared to the investment made. The classic ROI calculation formula provides a starting point for this evaluation:
ROI = (Total Value of Investment − Total Cost of Ownership / Total Cost of Ownership) ×100
Considerations for Evaluating ERP ROI
Business Growth:
An effective ERP system can facilitate business growth by providing scalable solutions that support increased demand, expansion into new markets, or diversification of product lines. Assessing the impact of ERP on revenue growth and market penetration is essential for calculating ROI.
Productivity Gains:
ERP systems streamline business processes, automate repetitive tasks, and provide real-time data insights, leading to significant productivity gains. When evaluating ROI, consider the time saved and the increase in output per employee to quantify the productivity improvements you’ve gained after ERP implementation.
Efficiencies:
Efficiencies achieved through ERP implementation include improved resource allocation, reduced manual effort, and optimised inventory management. Identify areas where ERP has streamlined operations and reduced waste to quantify the efficiency gains contributing to ROI.
Cost Savings:
ERP systems can lead to cost savings through various means, such as reduced inventory carrying costs, lower procurement expenses, and minimised operational inefficiencies. To quantify the direct and indirect cost savings attributed to ERP implementation you can use the ERP’s holistic view of your company to ascertain where any costs have been saved.
Other Aspects of Calculating ROI:
Here are a few other less obvious ways in which ERP implementation can aid your business. Whilst these are hard to quantify into ROI calculations, weighing up the entire array of benefits ERP provides is essential to understand it’s impact.
Reduction in Human Errors:
ERP systems minimise human errors by automating processes and ensuring data accuracy. This not only affects the day-to-day of your business but can also reduce the costs associated with rectifying mistakes and potential financial losses due to errors.
Avoided Project Delays:
By improving project management and resource allocation, ERP systems help avoid delays in project timelines, enabling timely completion and delivery of products or services. Assess the differences between annual project delays before and after implementation, to gain a comprehensive insight into how these affected your company’s ROI.
Access Coins ERP is an All-In-One Construction ERP Solution
Access Coins is our leading construction ERP that provides construction businesses with a sophisticated central system to plan, schedule and execute your projects.
Designed specifically to meet the challenges of the construction industry, Access Coins’ huge range of features gives you control over every part of the construction lifecycle.
With modules to help you manage your projects, workforce, financials and supply chain, Access Coins will transform your construction business.
Latest Construction ERP blogs and resources
Read our latest content on all things construction ERP software covering key industry questions and trends.