What Are the 5 Benefits of Modular or Off-Site Construction?
For over a century, the UK construction industry has relied on traditional, on-site building techniques.
But with the rapid development of construction technology and a growing demand for faster, more sustainable buildings, off-site construction, also known as modular or prefabricated construction, is transforming the industry.
This article explores the top benefits of modular construction, including reduced waste, increased efficiency, improved safety, and enhanced sustainability.
What is Modular Construction?
Modular construction involves manufacturing building components in a controlled factory environment before transporting them to the project site for assembly.
Traditionally, each element of a building, from the foundation to the final fixture, was created and assembled on location, often leaving construction projects vulnerable to delays, inefficiencies, and cost overruns.
By bringing the construction process indoors, modular techniques eliminate many of the uncertainties associated with on-site builds, such as weather disruptions, labour shortages, and waste.
This shift is enabling builders to meet growing demands in sectors like housing, healthcare, and education, where speed and scalability are critical.
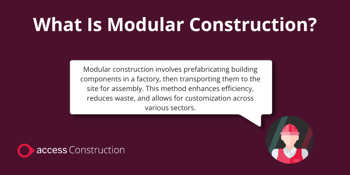
5 Benefits of Modular or Off-Site Construction
Modular or off-site construction has gained popularity because it offers clear, measurable benefits across the construction lifecycle, from planning to final assembly.
Here are the 5 core advantages of modular construction that are driving this transformation in modern building practices:
1. Reduced Waste and Increased Sustainability
Traditional construction is notorious for waste, with 32% of all construction waste being sent to landfill.
Off-site construction methods, on the other hand, significantly reduce material waste by taking place in a controlled factory environment where resources are managed efficiently, and material requirements can be accurately calculated. In this setting, materials are carefully measured and repurposed, leading to less leftover debris and minimising the environmental impact.
Additionally, modular construction has been shown to reduce greenhouse gas emissions by 17–30% compared to conventional construction methods.
Transportation requirements to the building site are also reduced, as fewer materials need to be transported separately.
Combined, these factors make modular construction an ideal choice for sustainable building projects, aligning with the global push for greener, more environmentally friendly practices.
2. Reduced Risk and Disruption
Construction sites are inherently hazardous, with risks such as falls, equipment malfunctions, and environmental hazards presenting constant challenges. Off-site construction relocates the bulk of labour-intensive work to a factory environment where conditions are more stable and safer.
By reducing on-site labour needs, this method helps minimise worker exposure to the unpredictable conditions found on traditional job sites, such as bad weather, limited visibility, and restricted space.
In addition to safeguarding workers, off-site construction is less disruptive to the surrounding community. The quieter, more streamlined assembly process on-site reduces pollution, traffic, and noise in populated areas, helping projects achieve better community relations.
3. Increased Efficiency and Project Speed
Modular construction is engineered for efficiency, with each stage of production taking place in a streamlined, organised factory setting.
By eliminating weather-related delays and other common disruptions, modular construction helps accelerate project timelines by up to 50%. The Construction Industry Training Board (CITB) also reports that modular projects typically achieve an 80% reduction in on-site labour.
Additionally, factories can operate year-round, meaning projects can be planned with precise timelines, making the process more predictable for stakeholders and reducing downtime.
4. Superior Quality Control
One of the standout benefits of modular construction is the ability to perform rigorous quality checks throughout the manufacturing process. Each module undergoes a thorough inspection before leaving the factory, ensuring high-quality craftsmanship and reducing the likelihood of defects.
By maintaining strict control over materials, assembly methods, and build standards, modular factories produce units that meet or exceed industry quality standards.
Factory-built modules are delivered 70–80% complete, often including mechanical, electrical, and plumbing systems as well as fixtures and finishes.
5. Cost Predictability and Financial Certainty
More than ever, construction cost overruns are a common concern for both developers and clients, often resulting from unexpected delays, material shortages, or fluctuating prices.
Modular construction helps address this challenge by providing a controlled, cost-stabilised production environment. As material needs and timelines are more predictable, it’s easier to manage budgets and anticipate costs.
This method allows clients to lock in design specifications and pricing before manufacturing begins, giving them greater financial certainty. Additionally, faster project completion times mean that buildings can be occupied sooner, allowing investors and developers to realise returns on their investments faster.
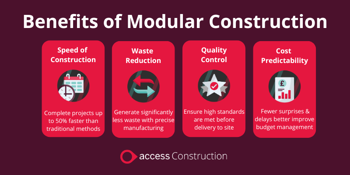
Access Coins – ERP Platform for Modular Construction
Developed by and for construction experts, Access Coins is an all-in-one ERP that covers everything from cost forecasting to workforce management.
5 Disadvantages of Modular Construction
While modular construction offers numerous benefits, to provide a complete overview we must touch on some of the challenges that can arise. Like any evolving construction method, understanding these potential obstacles is essential for industry professionals looking to optimise this innovative approach.
1. Regulatory Hurdles
Navigating the complex web of building codes and regulations can be a significant challenge for modular construction projects. Different regions may have varying requirements for factory-built structures, leading to delays in approvals and potential compliance issues.
Solution: Early engagement with local authorities and a thorough understanding of the regulatory landscape can streamline the permitting process. Utilising ERP systems can also help track compliance requirements and ensure all necessary documentation is in place.
2. Supply Chain Dependencies
Modular construction relies heavily on timely delivery of materials and components from various suppliers. Disruptions in the supply chain can delay production schedules and impact project timelines.
Solution: Implementing robust inventory management systems, can enhance visibility and control over the supply chain. Real-time data can help project managers identify potential bottlenecks and adjust procurement strategies proactively.
3. Transportation and Logistics
Moving large modular components from the factory to the construction site may presents logistical challenges to some projects. Without proper planning, transportation costs can be significant, and ensuring the safe delivery of modular units without damage is paramount.
Solution: Effective logistics planning and coordination with transport providers can minimise delays and costs. Optimising transportation routes and schedules, will help improve the overall efficiency of projects including modular construction.
4. Skilled Labour Shortage
The industry is facing a shortage of skilled labour, particularly in specialised areas that are frequently related to modular construction. This gap can hinder the successful implementation of modular projects.
Solution: Investing in training programs and partnerships with educational institutions can help build a skilled workforce. Additionally, leveraging technology, can help improve the quality of your supply chain.
5. Cultural Resistance
The current shift towards modular construction will likely continue to face resistance from traditional construction stakeholders who may be hesitant to adopt new methods and technologies.
Solution: Providing assurance, education and showcasing successful case studies can help mitigate this resistance. There is ample amounts of research out there on the benefits of modular construction. By engaging stakeholders early in the process and demonstrating the tangible benefits of modular construction, we can all help streamline the uptake in modular construction methods.
By proactively addressing these challenges, companies can better harness the potential of modular construction and create a more efficient, sustainable building process.
With the right tools and strategies in place, including the integration of ERP solutions, the construction industry can overcome these hurdles and fully realise the benefits of this innovative approach.
Modular Construction: 10 Key Questions Answered
1. Is modular construction only suitable for certain types of projects?
No, modular construction is highly versatile. It’s used across diverse sectors, including residential, commercial, educational, and healthcare, and can accommodate various designs and specifications.
2. Is modular construction cheaper than traditional construction?
Yes, in general, modular construction includes inherent efficiency and cost savings that help you save money over the course of a project. Additionally, fewer labour hours are required to complete a comparable traditionally-built project and waste is significantly reduced.
3. Does modular construction compromise building quality?
Not at all. Modular construction takes place in a controlled environment where quality control is rigorous, often surpassing traditional on-site standards due to consistent oversight and standardised procedures.
4. Can modular projects be customised to meet specific client needs?
Yes, despite common myths, modular buildings are fully customisable. Designs can be tailored to client preferences, including layout, aesthetics, and functionality, with many elements completed to client specifications in the factory.
5. How does modular construction impact project costs?
Modular construction often reduces costs by shortening project timelines and minimising material waste. Its predictability significantly decreases your chances of being hindered by delays that can add up in project costs. It also allows for better cost management and lowers the risk of budget overruns.
6. Is off-site construction better for the environment?
Yes, modular construction generally generates less waste, uses resources more efficiently, and reduces site disturbance and emissions, making it a more sustainable option than traditional methods.
7. Are modular buildings as durable as traditionally built structures?
Yes, modular buildings are designed to meet or exceed building code requirements and are highly durable. The controlled production environment in which they’re created enables robust construction and detailed inspections that add to a building’s longevity.
8. Can modular projects be financed and insured like traditional builds?
Yes, however it may take more effort on your part to find lenders and finance providers that understand modular construction. As a more recent construction method, some lenders and insurers may need help understanding the increased quality and stability of modular construction.
9. What are the transportation logistics for modular units?
Modular units are transported from the factory to the site in pre-built sections usually 80-95% completed. These sections are designed to fit on standard transport vehicles and can be assembled efficiently on-site with minimal disruption.
10. How does modular construction contribute to project timelines?
By enabling parallel site preparation and unit manufacturing, modular construction can reduce project timelines by up to 40%, allowing for faster project completion and earlier occupancy.