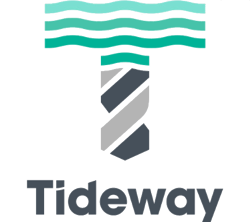
Super Sewer Deploys Gold-Star Cost Control With Access Coins
Access Coins ERP helped BAM Nuttall, Morgan Sindall & Balfour Beatty on their joint venture to deliver the £416 million section of Thames Tideway Tunnel.

Business size
Large

Industry
Infastructure

Product
Access Coins ERP
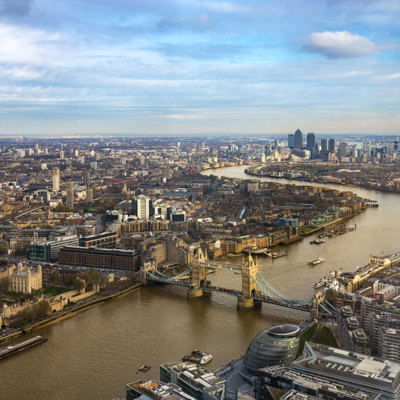
Challenge
- As a major infrastructure project fronted by three distinct companies, it was crucial that the project had a central approach for controlling costs – from procurement to project finance, commercial activities to operational teams
Approach
- BAM Nuttall, Morgan Sindall & Balfour Beatty implemented Access Coins Process Control Management System (PCMS)
Results
- With benefits ranging from cost savings to collaborative working, the PCMS tree has reduced aged debt and delayed payments by 30%, alongside a drastic reduction in processing errors
The Thames Tideway Tunnel, also known as the ‘Super Sewer’, is a major £3.8 billion project to construct a 25km tunnel under London’s River Thames to prevent tens of millions of tonnes of pollution entering the river each year.
The 25km tunnel will primarily be used to intercept, store and ultimately transfer sewage waste away from the River Thames. This will directly reduce the amount of waste and sewage entering the Thames, which historically could add up to tens of millions each year.
The three-way equal joint venture of BAM Nuttall, Morgan Sindall, Balfour Beatty (also known as BMB) was awarded £416 million to deliver the west section of the super sewer, running from Wandsworth in South West London to Acton in West London.
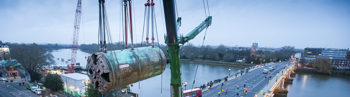
Moving From The Stone Age To The Digital Age With Access Coins
From the outset, the key priority of the finance team was to move their financial processes from ‘the stone age to the digital age’. With three major project partners involved in delivering this project, a common approach was required.
This approach would benefit from a common language, common processes, with common controls on a single unified system.
The team aimed to develop a 21st century solution from the very start of the project which was slick, quick, automated and obstacle-free.
The dangers of not deploying a single unified solution or an over-reliance on paper-based processes could not only result in huge administration burdens but also lead to critical errors. Disparate data or a breakdown of communication could lead to inaccurate data inputting, delayed or incorrect allocation of costs, and ultimately a lack of clarity on financial performance.

A New Approach To Process Control Management Systems (PCMS)
Imposing cost controls and increasing transparency is essential for construction businesses to work profitably. To start, the team focused on the vulnerable front end of project costs with the most financial risk: Purchasing.
E-requisition documents were implemented, tailored for specific budget allocations and self-populated with Work Breakdown Structure (WBS) codes. They would also include spending limits which were associated with the user’s role. By centralising these processes into a system which could be accessed by anyone, the relevant person could easily raise a requisition, minimising delays in the purchase process.
Next, the team looked at the development of project process controls, the PCMS Tree for which Access COINS would become the underlying central platform.
By having a system that prompts, guides and questions the user at the front end of the process we have greatly reduced escalating issues at the back end.
Automating Transaction Systems With Access Coins PCMS
Partnering with Access Coins, the teams developed and implemented automated transaction systems, as well as enhancing audit traceability. This helped reduce wasted time as well as reducing the administration burden which comes with manual paper processing.
Following this implementation, the joint venture now operates an automated 3-way match process, in which orders are called off using PCMS tree procedures, and suppliers are requested to submit electronic Goods Received Notes (GRN) and invoices using the Access Coins system.
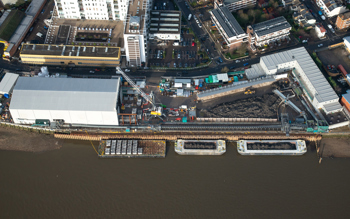
Developing New Approaches For Process Control Management With Access Coins
Where a standard three-way match formula is not applicable or practical, a new approach was developed called ‘Supplier Engagement for Bespoke Solutions (SEBS)’. This was designed to handle supplier purchase orders, front end delivery and costs by leveraging collaboration with both suppliers and operational teams.
Electronic call-off forms submitted from PCMS were confirmed by the supplier and returned directly into Access Coins. This supplier order confirmation created the line item and auto-generated the Goods Received Note (GRN) creating an automated two-way match.
This process ensures that costs have been captured accurately as well as reducing the need to manually input the GRN delivery ticket, whilst also increasing the volume of invoices being cleared without going into query.
Working against supplier live batching reports also helped save time and reduced churn, by producing more accurate accruals at cost period end, as well as reducing invoice queries and aged creditors.
Using Advanced Dashboards & Reporting To Unify Teams With Access Coins
A key challenge on this three-way venture project was to get both the suppliers and site-based construction teams on board.
This became bigger than just a process, and more about unifying teams and keeping everyone in the loop. This approach helped to remove obstacles with everyone having an understanding of the wider picture.
Regular site-based finance meetings, as well as mid-month site meetings with section managers and their core teams both increase engagement and are an opportunity to review reports such as ‘outstanding orders’ which are produced by Access Coins in advance of the formal month-end reports.
Simple to view, simple to use budget dashboards are designed to show commercial performance at a glance. They allow for data to be selected in various formats to measure commercial standing by identifying variations, risks and trends.
Furthermore, the Access Coins DSL (Detailed Source Listing) report is built into the background of the dashboard making it easy to drill down into the detail when needed.
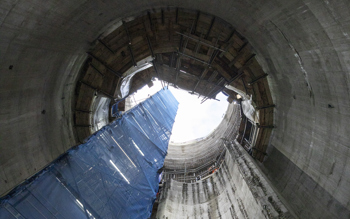
Modernising Process Management Control Systems (PCMS): A Success Story
Before implementing Access Coins, PCMS tree projects of this scale with a similar scope of works could average around £950,000 to £1,200,000 of aged debt. Over 45% of this could be attributed to invoices being delayed or on-hold because of missing paper delivery tickets.
However, since the Access Coins implementation aged debt for this project is now averaging at 15%.
This has resulted in 30% fewer delayed invoice payments through missing paperwork.
Additionally, supply chain disputes such as incorrect rates and quantities on invoices have been reduced from 30% to 10%.
The introduction of PCMS processes with Access Coins has also greatly reduced human error – for example, incorrectly coded requisitions and call off forms plagued with incorrect cost codes have reduced on average from 17% to around 0.5% of the project monthly cost turnover.
PCMS and Access Coins solutions enable real-time expenditure reports to be visible throughout the project, providing complete transparency from start to finish.
Access Coins has also helped the teams being to tackle their over-reliance on paper-based processes, which have now been dramatically reduced.
In a fast-changing commercial world, improved efficiency, compliance, profitability, happier staff and clients are critical success factors. Partnering with Access Coins will help your construction business increase productivity and grow within a competitive sector.
