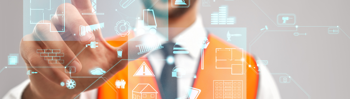
The importance of centralised management
No two sites manage maintenance the same way. One location may log work orders in spreadsheets while another uses email and some may even still rely on verbal requests.
This patchwork of processes can start to create chaos in your operation such as missing tasks, duplicating admin and causing delays. Without a central process in place, recurring equipment issues might go unnoticed, repairs can take longer and compliance checks are harder to track.
Centralising everything changes that as it puts all tasks, requests and data in one place. Teams will follow a single process, no matter the location and managers don’t have to constantly chase for updates. Inspections are completed on time and if something urgent comes up, it gets prioritised fast.
Take a hotel group, for example. When each site handles maintenance differently, you lose visibility. A recurring issue at one property could slip through the cracks because there’s no shared record. But with a centralised approach, maintenance is tracked consistently across all locations. You can plan ahead, allocate resources efficiently and avoid costly surprises.
In an industry like hospitality, where equipment failures can quickly affect service, this consistency is essential. A centralised system not only prevents problems but also saves time by reducing admin work. The result? Smoother operations, fewer disruptions and better control over long-term costs.
This isn’t just about convenience; it’s a way to future-proof operations. Facility management software offers managers an easy way to track all maintenance activities in real time. Rather than jumping between spreadsheets or waiting for status updates from team members, the right solution lets you make faster, data-driven decisions instead. Businesses that centralise their operations often find they can significantly reduce downtime, improve service levels and keep costs under control.
Automating and scheduling maintenance
When your maintenance schedule relies on manual processes, delays are bound to happen. Inspections get missed, urgent repairs take longer and keeping track of tasks becomes time-consuming which can add up over time.
Automated scheduling helps you avoid these issues by keeping things on track without constant oversight. Teams know exactly what needs to be done and when, with reminders that keep checks and tasks moving forward. This means fewer delays, fewer surprises and more efficiency..
One hotel group we have worked with was struggling with recurring equipment failures due to inconsistent maintenance. Tasks were logged manually, which often led to missed inspections. By introducing an automated task management system, each site followed a unified plan with regular updates sent to staff. The improvements were immediate as their downtime dropped, and repairs became more manageable.
By automating routine tasks, you’re not just preventing breakdowns. You’re also maintaining compliance without extra admin work. Tools like Access Maintain ensure inspections are completed on time, with progress updates tracked centrally. That way, managers always have the information they need, right when they need it.
Leveraging data for better decision-making
Maintenance decisions shouldn't be based on guesswork. The right data helps facility managers plan ahead, optimise resources and prevent downtime. It shifts the focus from reacting to problems and preventing them before they happen.
For example, maintenance logs can reveal patterns—like equipment in one location breaking down more often than at others. Without data to track these trends, you risk repeated failures and emergency repairs that could have been avoided.
With access to real-time data, managers can see exactly where bottlenecks occur. Is one site consistently slow to resolve work orders? Are inspections being missed? Knowing these details makes it easier to adjust resources and processes. Data can also highlight early warning signs, like gradual performance drops in critical equipment, giving teams time to intervene before a breakdown.
This isn’t just about crisis management—it’s also a way to cut costs. By using data to schedule preventive maintenance, businesses can extend equipment life and reduce unplanned repairs. Managers no longer have to rely on manual updates or spreadsheets to stay informed. A good computer-aided facility management (CAFM) solution can provide detailed reports on maintenance activity, compliance and asset performance, all in one place.
Hospitality businesses that take a data-driven approach often find that they can prevent small issues from turning into expensive disruptions. And with less time spent chasing information, managers can focus on running smooth, efficient operations across all sites.
Ready to simplify your facility management?
Managing maintenance gets a whole lot easier when you've got access to the right tools. In this article you’ve seen how centralising processes, automating key tasks and using real-time data can reduce downtime and improve efficiency and that's all easier to do with facility management software.
Access Maintain lets you manage all your sites from one place. Tasks get scheduled and tracked automatically,updates happen in real time and compliance checks are always visible when you need them.
If you’re curious to see more:
Watch our demo video to see Access Maintain in action
Download our Property Maintenance Brochure to learn more
Take the stress out of multi-site maintenance—let’s make facility management work for you.