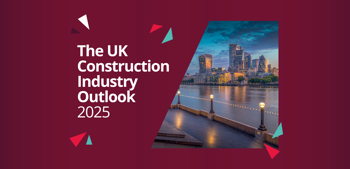
Well-documented challenges from 2024 such as persistent labour shortages continue to strain project schedules and profitability. Disruptions to global supply chains and a turbulent economic environment are also slated to increase building costs by 15% over the next five years, according to the BCIS.
Yet despite these hurdles, there are reasons to remain optimistic. Innovation is accelerating across the industry, with breakthroughs in construction technology, and an increase in projected overall construction output and increased government funding.
Labour Shortages: Impact and Strategies for Adaptation
Labour shortages remain one of the most significant challenges facing the UK construction sector. Recently, the latest Construction Skills Network (CSN) report, cited that around 225,000 new construction workers are needed in the UK by 2027 to fill demand.
Increased investment in infrastructure, housing developments, and major projects has heightened the demand for both skilled and unskilled labour, further widening the workforce gap.
Several factors contribute to the labour shortage, including an aging workforce, skill mismatches, and difficulties attracting younger generations. Research conducted by Search Consultancy identified a lack of qualified candidates as a primary cause of the shortage (36%) and highlighted staff retention as another significant challenge in the industry (25%).
Meanwhile, evolving skill requirements, particularly for digital and technical roles, create additional complexity as firms adapt to a more automated and technology-driven construction landscape.
Addressing these challenges will require construction firms to adopt innovative strategies, including:
Leveraging AI and Digital Tools
In 2025, construction companies should focus on integrating AI-enabled automation, robotics, and other digital software tools to help bridge labour gaps by boosting productivity and reducing reliance on physical labour.
Technologies like automated project management systems, autonomous machinery, and augmented reality (AR) for on-site tasks can streamline operations, all whilst attracting younger workers interested in tech-forward industries.
Engaging, Upskilling and Career Development Initiatives
Offering training opportunities such as cross-skilling, on-the-job mentorship, and digital learning programs can equip workers with the skills needed to thrive in modern construction environments.
The industry should also focus on increasing awareness about the potential within construction careers. The lack of interest from younger generations in construction careers is compounded by misconceptions about the construction industry. These include beliefs that roles are perceived as too physically demanding, offer little-to-no career advancement and low pay.
Exploring Alternative Talent Pools
Recruiting from outside the construction sector, including candidates transitioning from technology, manufacturing, or other industries, could offer construction firms a fresh approach to sourcing talent.
As the industry evolves to accommodate innovations in tech and AI, so too does the skill-gap within the industry. By putting more focus on talent pools from outside the construction sector, alongside investing in diversity and inclusion initiatives, construction can widen its talent pool by encouraging underrepresented groups, such as women or young graduates, to explore careers in construction.
Rising Material Costs: Challenges and Solutions
Rising material costs remain one of the most significant factors affecting project budgets and timelines in the UK construction sector.
As demand for new housing, infrastructure, and commercial developments continues to rise, the industry faces ongoing price pressures across essential building materials, including steel, concrete, timber, and insulation.
These challenges are being compounded by supply chain disruptions, environmental regulations, and the push for sustainability.
Key Materials Impacted:
- Steel: Volatile steel prices continue to impact the sector, driven by global supply chain issues, energy costs in manufacturing, and tariffs.
- Concrete: The transition towards eco-friendly concrete with a lower carbon footprint is increasing production costs, reflecting the adoption of newer, greener technologies.
- Lumber: Lumber prices have surged in response to high demand for housing and supply chain constraints across international markets.
- Insulation Materials: With the rise of energy-efficient and green buildings, insulation materials are increasingly in demand, adding further pressure to costs.
While sustainable and eco-friendly materials are becoming critical for meeting green building targets, their higher price points present an added challenge. However, contractors and developers can adopt several approaches to address rising material costs:
The latest Construction Market Insights Report from global consultant Linesight predicts that copper, which hit an all-time high in Q2 2024, is expected to rise a further 2.2% by 2025. They also cite that lumber prices are set to increase because of the government’s new housing targets, which could have a knock-on effect to other materials such as plasterboard.
The Future Homes Standard 2025
The Future Homes Standard (FHS) is set to revolutionise the way new homes are designed and built in the UK, marking a significant step forward in the country’s journey to achieving net-zero carbon emissions by 2050.
What is the Future Homes Standard?
The FHS aims to ensure that all new homes built from 2025 will produce 75-80% fewer carbon emissions compared to those constructed under current Building Regulations.
The primary focus will be on decarbonising heating systems, improving energy efficiency, and enhancing the overall sustainability of homes.
Key Measures of the Future Homes Standard:
- Low-Carbon Heating Systems: Technologies such as heat pumps will replace traditional gas boilers, slashing carbon emissions and offering more energy-efficient alternatives.
- Fabric Efficiency: New builds will feature high-quality insulation, airtight structures, and triple-glazing to minimise heat loss and enhance energy efficiency.
- Reduced Energy Waste: Innovations in hot water systems, ventilation, and building materials will work together to create homes that are both greener and more cost-effective for occupants.
Why the Future Homes Standard Matters:
Heating and powering buildings currently account for 30% of the UK’s total energy usage. By implementing the FHS, the government aims to dramatically reduce this figure, aligning new housing developments with the UK’s ambitious net-zero emissions target.
Implementation Timeline:
The Future Homes Standard rollout follows a phased approach:
- 2023: Technical consultations and policy development began, focusing on the specific standards homes must meet.
- 2024: Implementation consultation to finalise regulations for compliance.
- 2025: Full enforcement of the Future Homes Standard, requiring all new homes to comply with updated Building Regulations.
Building Safety Act 2022 Beds Down
Building safety remains a high priority in the UK, with the Building Safety Act 2022 (BSA) continuing to reshape the regulatory environment for higher-risk buildings (HRBs).
While its main provisions came into force in October 2023, the construction industry will see further developments in 2025 as the legislation beds in.
Key Takeaways of the Building Safety Act
- Gateway 2 Approval Process: Developers must obtain building control approval from the Building Safety Regulator (BSR) before construction begins on HRBs. The approval process ensures that the proposed design meets stringent safety requirements.
- Enforcement and Compliance: The BSR is increasingly active in monitoring and addressing building safety concerns. The first enforcement actions are expected in 2025.
Current Challenges Facing the Building Safety Act
A recent report by Inside Housing, based on data from a Freedom of Information request submitted by the Fire Association, has revealed challenges in the Gateway 2 approval process:
- From October 2023 to September 2024, only 14% of applications for HRBs were approved as compliant.
- Delays may stem from capacity issues within the BSR, a surge in applications, and a lack of clarity surrounding application requirements.
What Could This Mean for You?
The stringent provisions under the Building Safety Act necessitate a focus on regulatory compliance, transparent communication, and proactive planning for higher-risk projects. In 2025, firms can expect:
- Increased oversight and enforcement activity from the BSR.
- Continued learning and adaptation as the BSA provisions are integrated into construction workflows.
- Greater accountability for building safety and design standards.
Construction Technology Innovations in 2025
The construction industry is on the brink of a technology revolution, with tools like Building Information Modelling (BIM), Digital Twins, robotics, drones, and blockchain driving efficiency and sustainability.
As regulatory demands grow, firms must adopt innovations to remain competitive.
Accelerating BIM Adoption
With 73% of UK construction processes already utilising Building Information Modelling (BIM) in 2020, BIM has long been a transformative tool, yet adoption remains inconsistent. The shift from Level 2 to Level 3 BIM, with its emphasis on lifecycle management and operational data, will force firms to modernise processes.
Smaller companies will need support to meet client expectations and regulatory requirements as BIM begins integrating with AI and smart sensors, enabling smarter design and project delivery.
The Role of Digital Twins
Digital Twins offer immense potential for improving real-time monitoring, project efficiency, and sustainability by creating virtual replicas of physical assets.
Despite this, barriers like high costs and skills shortages may leave SMEs trailing larger players unless they receive adequate support. Firms that harness this technology can reduce errors, optimise planning, and lower carbon emissions.
Blockchain for Greater Transparency
While the adoption of Blockchain is still in its early stages, this technology can revolutionise supply chain transparency and streamline smart contracts for faster payments.
While early-stage adoption remains a hurdle, firms investing in this technology will benefit from improved collaboration and efficiency, critical in public and large-scale projects.
By 2025, companies that adopt blockchain technology could achieve a substantial competitive advantage, especially in managing large-scale, complex projects and public sector contracts.
Digital Transformation with ERP Software
As the construction industry evolves, ERP systems offer a vital tool for future-proofing businesses in a rapidly changing environment. By facilitating the integration of emerging technologies such as BIM and Digital Twins, ERP systems enable construction companies to manage projects more efficiently, reduce risks, and enhance data accuracy.
For small and medium-sized enterprises (SMEs), ERP acts as a bridge to digital transformation, breaking down barriers such as limited skills and resources. These systems empower teams to harness the full potential of technological advancements, fostering competitiveness and long-term sustainability.
By centralising data and automating processes, ERP systems provide a streamlined approach to managing complex projects, from procurement through to financial tracking.
For construction companies looking to remain at the forefront, choosing an ERP system that supports growth, efficiency, and innovation is crucial. With the right solution in place, businesses can navigate the evolving landscape with confidence, optimise their workflows, and ensure that their operations are built to last.
Overcome 2025’s Challenges with Access Construction
Access Construction’s software moves businesses away from spreadsheets and outdated systems to cloud-based solutions that streamline processes and encourage growth.
Access Coins is a construction-specific ERP software which helps construction companies take control of their cashflow, save time and cut costs by centralising your data.
Access ConQuest is our leading construction estimating software which creates accurate estimates, fast. Access ConQuest is also packed with features to help companies win more projects such as sourcing subcontractor quotes and quickly acquire measurements through takeoff.