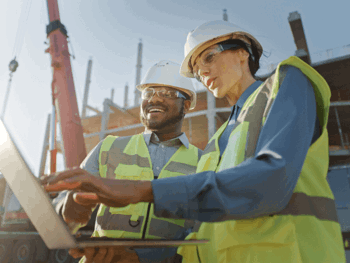
In today's construction landscape, we are seeing an increasing focus on practices that minimise environmental impact.
In the UK, construction activities contribute significantly to carbon emissions and waste generation, with reports showing that the UK C&I sectors generated 40.4 million tonnes of waste in 2020.
An approach that is gaining traction is deconstruction—a method that diverges from traditional demolition practices by systematically disassembling structures to salvage materials for reuse or recycling.
What Is Deconstruction In Construction?
Deconstruction in construction is a demolition method with an emphasis on the meticulous dismantling of a building, rather than wholesale destruction. Unlike demolition, which often involves the indiscriminate razing of disused structures, deconstruction prioritises the careful disassembly of buildings to salvage valuable materials.
The deconstruction process involves the systematic removal of components such as fixtures, fittings, and structural elements, with the aim of preserving their integrity for reuse or recycling.
Demolition Vs Deconstruction
Demolishing disused buildings can often be seen as the quickest and most straightforward way to approach the problem. However, it isn’t always the best course of action in the long run. Let’s look at the key differences between the two and weigh up their benefits.
Demolition:
Traditional demolition practices typically involve the swift and comprehensive destruction of structures using heavy machinery and controlled explosives. While efficient in terms of time and cost, demolition often results in the generation of substantial waste and debris. Materials that could otherwise be repurposed or recycled are frequently lost in the process, contributing to environmental degradation and resource depletion.
Deconstruction:
Deconstruction approaches the task of dismantling buildings with a focus on salvaging materials and maximising resource utilisation. By carefully disassembling structures piece by piece, deconstruction allows for the recovery of valuable materials such as timber, metal, and masonry. This method not only reduces the volume of waste destined for landfills but also facilitates the integration of reclaimed materials into future construction projects, thereby promoting sustainability and circular economy principles.
The Pros and Cons Of Deconstruction & Demolition
|
Demolition |
Deconstruction |
Pros |
- Rapid and cost-effective |
- Enables the recovery of valuable materials |
|
- Suited for projects with tight timelines |
- Supports sustainability objectives |
|
- Minimal labour requirements |
- Reduces environmental impact and landfill burden |
Cons |
- Generates significant waste |
- Generally slower and more labour-intensive than demolition |
|
- Limited opportunities for material reuse or recycling |
- May incur higher upfront costs |
|
- Potential environmental and community impacts due to noise, dust, and debris |
- Requires careful planning and coordination to optimise material recovery and project efficiency |
The Types of Deconstruction in Construction
There are two main types of deconstruction methodologies commonly employed today. These are selective deconstruction, often referred to as soft-strip, and whole-house deconstruction.
Selective Deconstruction (Soft-Strip):
Selective deconstruction involves removal of obviously valuable components and materials from a structure before its complete demolition. This process involves carefully extracting fixtures, fittings, and other salvageable items, such as doors, windows, and architectural features.
Soft-stripping targets the most easily obtainable items in an effort to minimise waste generation, making it an efficient and sustainable option for renovation and redevelopment projects.
Whole-House Deconstruction:
Not to be fooled by the name, this type of deconstruction can apply to any type of building. Whole-house deconstruction involves a more comprehensive approach to dismantling buildings, emphasising the systematic disassembly of entire structures with the goal of salvaging as much material as possible.
Unlike traditional demolition, which often results in the loss of reusable resources, whole-house deconstruction prioritises the careful separation and preservation of materials for reuse, recycling, or repurposing. The materials are therefore saved from landfill and can be processed and reused in future build works.
Simplify Deconstruction with Access COINS ERP
Access COINS ERP is an industry-leading solution which helps construction professionals plan and execute complex projects such as deconstruction efforts. By providing a single source of truth for your data, Access COINS provides accurate, real-time costs and forecasts, alongside a wealth of features built for the construction industry.
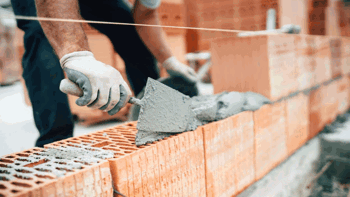
What are the Benefits of Deconstruction in Construction?
Deconstruction offers a multitude of benefits specifically around the principles of sustainability and resource efficiency. In recent years this has made deconstruction an increasingly attractive option for construction projects operating under increased scrutiny from the public and government regulations.
Resource Conservation:
By salvaging materials from existing structures, deconstruction helps conserve valuable resources such as timber, metal, and masonry. These materials can be reused in subsequent construction projects, reducing the demand for new raw materials and mitigating the environmental impact of resource extraction.
Waste Reduction:
Unlike traditional demolition, which often results in large quantities of waste sent to landfills, deconstruction minimises waste generation by selectively dismantling structures and separating materials for reuse, recycling, or repurposing. This diversion of waste from landfills contributes to overall waste reduction and promotes a circular economy.
Environmental Preservation:
Deconstruction contributes to environmental preservation by reducing carbon emissions associated with the manufacturing and transportation of new building materials. Additionally, salvaging materials prevents the release of harmful substances into the environment that may occur during demolition activities.
Cost Savings:
While deconstruction may require more labour and time compared to demolition, the potential cost savings associated with material reuse and recycling can offset these inflated upfront costs, which could have a positive impact on construction company profit margins.
Moreover, long-term benefits, such as reduced waste disposal fees and enhanced public perception of sustainable practices, can contribute to the overall cost-effectiveness for UK construction businesses.
Community Engagement:
Deconstruction projects provide opportunities for community engagement and involvement, particularly in areas with a focus on historic preservation or sustainable development. Collaborating with local organisations or employing skilled labour from the community can foster positive relationships and promote social responsibility within the construction industry.
What are the Drawbacks of Deconstruction?
Whilst deconstruction offers numerous advantages, it is essential to address the potential drawbacks associated with this approach.
Increased Time and Labour Requirements:
Deconstruction typically requires more time and labour compared to traditional demolition methods. The disassembly of structures and the careful separation of materials demand skilled labour and meticulous planning, which can prolong project timelines and increase labour costs.
Higher Upfront Costs:
Implementing deconstruction may involve higher upfront costs compared to demolition, primarily due to the additional labour and resources required for salvaging materials and managing waste. While the long-term benefits of material reuse and waste reduction can offset these initial expenses, the upfront investment may present a barrier for some projects.
Logistical Challenges:
Deconstruction projects may encounter logistical challenges related to the handling, transportation, and storage of salvaged materials. Coordinating the removal and transport of materials to recycling facilities or storage locations requires careful planning and coordination, particularly for large-scale projects or sites with limited access.
Risk of Damage to Salvaged Materials:
Less of a drawback and more a word of caution, during the deconstruction process, salvaged materials may be susceptible to damage or degradation if not handled carefully. Factors such as weather exposure, improper handling, or inadequate storage conditions can diminish the quality and value of salvaged materials, reducing their potential for reuse or recycling. Therefore, the utmost care should be taken to ensure the materials salvaged are appropriate for future use.
How can Construction ERP Software Help with Deconstruction Projects?
Construction-specific ERP (Enterprise Resource Planning) software can play a pivotal role in facilitating the efficient planning and management of deconstruction projects. By integrating various functionalities and streamlining project workflows, ERP software offers several benefits for contractors and construction companies:
Resource Allocation: ERP software enables contractors to efficiently allocate resources such as labour, equipment, and materials to deconstruction projects. With real-time visibility into resource availability and utilisation, project managers can optimise resource allocation to maximise efficiency and minimise costs.
Project Planning and Scheduling: ERP systems provide robust project planning and scheduling capabilities, allowing contractors to create detailed timelines and milestones for deconstruction projects. By effectively sequencing tasks and allocating resources, construction companies can ensure timely project completion while minimising disruptions.
Material Tracking and Inventory Management: Deconstruction projects involve the salvaging and recycling of materials, making accurate material tracking and inventory management essential. ERP software enables contractors to track the movement and utilisation of materials throughout the project lifecycle, ensuring transparency and accountability in material management.
Cost Control and Budgeting: With built-in financial management modules, ERP software enables contractors to effectively control costs and adhere to project budgets. By tracking expenses, managing subcontractor payments, and generating accurate financial reports, construction companies can maintain financial transparency and accountability throughout the deconstruction process.
Compliance and Documentation: ERP systems streamline compliance management by centralising documentation, permits, and regulatory requirements for deconstruction projects. By ensuring compliance with environmental regulations and safety standards, construction-specific ERP software helps mitigate risks and avoid potential liabilities associated with deconstruction activities.