What is Procurement in Construction? Procurement Process, Methods and Contracts
Procurement in construction refers to the process of acquiring all the necessary goods and services required to complete a construction project. This includes everything from materials like concrete and piping to services like electrical work and plumbing.
In this article, we look at procurement methods in construction, procurement contracts, a step-by-step look at the procurement process and tips on how to improve construction procurement.
What Is Procurement In Construction?
Procurement in construction refers to the crucial process of acquiring the necessary goods and services to successfully accomplish a construction project. It involves meticulously selecting the most suitable contractual arrangement, inviting bids, and finalising the essential contracts needed to initiate the project.
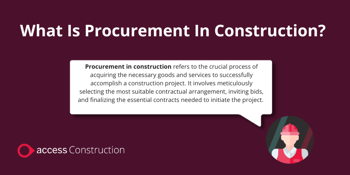
Key aspects of procurement in construction include:
- Identifying Needs:
Determining the exact materials, equipment, and services required for the project.
- Selecting Suppliers:
Choosing reliable and cost-effective suppliers and contractors.
- Negotiating Contracts:
Establishing clear terms and conditions for purchases and services.
- Purchasing and Logistics:
Managing the purchase and delivery of materials and equipment.
- Quality Control:
Ensuring that all procured items meet the project's quality standards.
- Cost Control:
Managing budgets and expenses related to procurement.
Because of the many various professionals involved in a project - surveyors, designers, architects, suppliers and more - a clear procurement strategy is critical to a successful project.
Effective procurement will ensure that all the necessary materials and services are available to complete a project on time, within budget and to the required quality standards.
Selecting the right procurement route for a project can improve long-term supplier relationships and help mitigate risk by putting contractual protections in place.
There are many different procurement routes to choose from, so it is important to consider long-term business goals when selecting a procurement strategy.
What Is The Procurement Process In Construction?
The procurement process in construction is crucial for the successful completion of a project. It involves a series of steps to acquire the necessary goods and services. Here's a breakdown of the process:
- Project Planning and Requirements Definition
- Supplier Research and Selection
- Procurement Strategy Development
- Bid Solicitation and Evaluation
- Contract Award and Management
- Delivery and Inspection
- Payment and Closure
Project Planning and Requirements Definition
This is the phase where a project scope is defined (and potential scope changes are outlined). Procurement professionals then determine the specific materials, equipment, and services required for the project. Preconstruction teams then create a detailed list of materials and quantities needed, and finance teams allocate funds for procurement activities.
Supplier Research and Selection
Procurement teams now identify potential suppliers for required materials and services. Suppliers are assessed based on factors like quality, price, delivery time, reliability, and financial stability.
Pre-qualification assessments are completed to ensure suppliers meet project requirements.
Procurement Strategy Development
At this phase, the appropriate procurement method (lump sum, cost plus fee, unit price, etc.) is chosen based on project requirements. Preconstruction teams must create a detailed plan outlining procurement activities, timelines, and responsibilities, including identifying risks.
Bid Solicitation and Evaluation
Construction professionals must now develop clear and concise bid documents, including specifications, drawings, and terms and conditions and send to pre-qualified suppliers. Bids are evaluated based on price, quality, delivery, and other factors.
Contract Award and Management
Owners or contractors must now select the winning bidders and award the contracts. Contract performance is now consistently assessed, including monitoring deliverables, payment schedules, and change orders.
Delivery and Inspection
This phase involves the scheduling and coordination of the delivery of materials and equipment. Delivered materials need to be inspected to ensure they meet project specifications.
Payment and Closure
Owners or contractors must ensure timely payment to suppliers according to contract terms. Contracts are finalised and procurement activities closed out upon project completion.

What are Procurement Contracts in Construction?
A procurement contract outlines the pricing mechanism that will be used depending on the amount of risk both the owner and contractor/supplier are willing to take.
There are many types of contracts and structures that might be used determined by the size and complexity of a project.
There are many types of procurement contracts used in the construction industry, some of the most used being:
Lump Sum (Fixed Price) Contract
A lump sum, or fixed price, construction contract is an agreement where the contractor commits to completing the entire project for a predetermined, fixed amount of money.
This means the owner knows exactly how much the project will cost upfront, regardless of any potential cost overruns.
These contracts must have a clear project scope to avoid project disputes down the line, and are open for contractors to bid on.
Contractors take on more risk with a fixed-price contract, but if there is a clear scope of work, contractors can potentially make higher profits with good planning and cost control. Financial management of fixed price contracts is also more straightforward.
Cost Plus Fee Contract
A cost plus fee construction contract is an agreement where the contractor is reimbursed for all the actual costs incurred in completing the project, plus a predetermined fee for their services.
This fee is typically a fixed amount and does not vary based on the project's final cost.
Risks are shared between owner and contractor, and contractors are protected from cost overruns. This contract is more flexible for scope changes.
Unit Price Contract
A unit price contract is a type of construction contract where the contractor provides a price for each unit of work to be performed. This differs from a lump sum contract where the total price for the entire project is fixed.
The contractor specifies a price for each measurable unit of work (e.g., cubic meter of concrete, square meter of flooring). The project's total cost is determined by multiplying the unit price by the actual quantity of work completed.
Unit Price contracts are adaptable to changes in project scope or quantities, and are more likely to be used in projects with uncertain scope such as infrastructure.
Streamline Construction Procurement with Access Coins ERP
Access Coins is a leading ERP software for construction built to help streamline the procurement process.
What are Procurement Methods in Construction?
A procurement method is the route in which both the design and construction work is procured. The method chosen should align with the client's long-term business goals.
There are many different procurement methods to choose from with influencing factors of speed, cost, quality and risk to consider. The main procurement methods in construction are:
Traditional Procurement (Design-Bid-Build)
This is traditionally the most common procurement method in construction. It involves three distinct phases:
Design Phase - The owner hires a design team (architects, engineers) to develop detailed plans and specifications for the project. This phase focuses on defining the project scope, creating design concepts, and producing construction documents.
Bid Phase - The owner invites contractors to submit bids based on the completed design documents. Bids are typically chosen based on price and other factors like experience, qualifications, and safety record.
Build Phase - The selected contractor is responsible for constructing the project according to the design documents. The owner oversees the project to ensure it meets the specified requirements.
While DBB is a well-established procurement method, it's important to note that alternative procurement methods like Construction Management have gained popularity due to their potential advantages in terms of time, cost, and quality.
Design-Build
Design-Build is a construction procurement method where a single entity is responsible for both the design and construction of a project. This contrasts with the traditional design-bid-build method, which separates these two phases.
With the contractor accountable for both design and construction, this method can lead to a faster and smoother delivery.
Construction Management
Construction Management (CM) is a procurement method where the owner hires a construction manager to oversee the project rather than a general contractor. The construction manager acts as the owner's representative, coordinating subcontractors and managing the project.
The owner directly contracts with a construction manager to oversee the project. The owner contracts directly with subcontractors for various trades (electrical, plumbing, etc.). The construction manager provides then expert advice and manages the project on behalf of the owner.
This allows the owner to have more direct control over the project but requires more active involvement in the project.
Public-Private Partnership (PPP)
A Public-Private Partnership (PPP) is a contractual arrangement between a government entity and a private company to finance, design, construct, and sometimes operate a public facility. This collaborative approach aims to leverage the strengths of both the public and private sectors to deliver projects more efficiently and effectively.
PPP projects include highways, bridges, hospitals, schools, and public transportation systems.
PPPs typically involve long-term contracts, often spanning decades. Contracts often include performance metrics to ensure the project meets specific standards.
Integrated Project Delivery (IPD)
Integrated Project Delivery (IPD) is a collaborative project delivery method that brings together key parties involved in the design, fabrication, and construction of a project under a single agreement. This approach fosters open communication, shared risk, and a focus on achieving project goals.
All key stakeholders (owner, designer, builder, subcontractors) are bound by a single contract and are involved from the project’s inception. Project participants share in both the potential profits and losses.
While early involvement and collaboration lead to faster project delivery, developing and managing a single agreement for multiple parties can be challenging.
Turnkey
A turnkey procurement method is a comprehensive approach where a single contractor assumes complete responsibility for a project from its inception to completion. This includes design, construction, and often even financing, equipment, and labour.
The contractor is solely accountable for the entire project, and the client receives a fully operational facility or product ready for immediate use. Often, a fixed price contract is used, providing cost certainty for the client.
However, modifying the project after the contract is signed can be complex and costly.
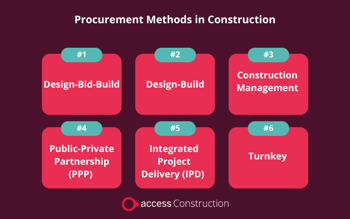
How to Choose a Construction Procurement Method
Selecting the appropriate procurement method is a critical decision that can significantly impact a construction project's success. Several factors should be considered include project complexity, risk tolerance, project scope, market conditions, project schedule and budget constraints.
For example, simple projects might benefit from traditional design-bid-build. Whereas complex projects may require a more collaborative approach like design-build or construction management. Projects with uncertain scope might benefit from the cost-plus or construction management, as design-bid-build relies on clear scopes.
How Does ERP Transform the Construction Procurement Process?
The construction procurement process is a complex one, involving countless data points and decisions to be made. ERP systems like Access Coins create a single source of truth for all procurement data, including supplier information, material costs, contracts, and purchase orders.
This eliminates data inconsistencies and ensures everyone has access to the same information.
Many procurement tasks, such as purchase requisition approval, purchase order generation, and invoice processing, can be automated within an ERP system, reducing manual effort and errors.
Access Coins ERP also facilitates supplier onboarding, performance tracking, and contract management, streamlining the supplier-relationship management process.
Construction ERP also provides valuable insights into procurement performance through detailed reports and analytics, enabling data-driven decision-making.