How To Avoid Rework In Construction
Rework is not only a huge source of frustration within the construction sector, but can lead to devastating losses in both time and money on a project, no matter the size and scale. It is estimated that in Australia and New Zealand, $14.2 billion was spent on rework in 2018.
This article looks at the leading causes of rework and identifies practical ways that construction professionals can reduce the amount of rework required within in a construction project, from the design phase through to completion.
What Is Rework In Construction?
Rework is the name given to any work within a construction project which has to be done again due to poor quality, or the original work does not comply to standards set in the plan or contract.
All rework, by definition, is unplanned and not taken into account within an existing schedule and budget. Rework includes the deconstruction of work done in order to correct the mistakes made.
Rework occurs for a number of reasons, including design errors or inaccuracies in the original work.
The majority of construction work will include rework, and it is vital for construction firms to try and keep rework to a minimum.
The Cost Of Rework In Construction
While studies into the total cost rework accounts for have varied results, an Australian research report in 2018 revealed rework reduced yearly profits by 28% with an average cost of 0.39% of project contract value.
Construction rework is a huge threat to any contractor’s bottom line, with time delays and added costs often including more labour, materials and equipment than previously budgeted and exposure, in some cases, to liquidated damages.
Rework can also have a domino effect on project costs, as schedules change to take rework into account and subcontractors may require additional site management to resolve identified issues.
Rework can also lead to damaged relationships and serious tensions between team members, leading to further impacts on productivity and budgets. This can damage a contractors’ reputation among employees, subcontractors and clients.
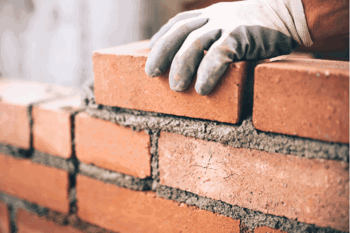
What Are The Causes of Rework In Construction?
There are many causes of rework which can be found in every phase of a construction project.
Causes of Construction Rework In Design Phase
- Poor structural design – the project’s initial design does not work or meet government regulations.
- Design errors – errors and omissions within the design can then lead to changes mid-project which require rework.
- Design changes – one of the most common causes of rework, design changes will need more rework the later they occur in the project.
Causes of Construction Rework In Procurement Phase
- Bad quality materials – the materials procured for the project are not up to the standards set by the client.
- Poor subcontractors – trades on a project do not complete work to the standard set within their agreement or are underqualified.
Coordination and Project Management Causes of Construction Rework
- Inadequate planning – if not enough time is spent on the preconstruction phase, where a project is laid out and planned, mistakes can be made and details can be missed which will lead to rework further down the line.
- Poor document control – team members on a project do not have access to the information they need due to not getting essential documentation on time, or at all.
- Poor communication – workers are not informed regularly about project progress or changes, leading to costly miscommunication.
- No quality control – a lack of process around quality control and quality assurance can easily lead to work which is not up to standard.
- Bad data – A 2021 study by FMI Consultants found that 14% of all construction rework across the previous year was caused by inaccurate data.
On-Site Causes of Construction Rework
- Lack of supervision – on-site supervisors or project managers do not spot mistakes as they happen on-site.
- Inefficient safety training – poorly trained workers who are not informed of health and safety measures are more likely to make mistakes which could lead to rework or, even worse, harm to those working on-site.
- Unavailability of materials – the recent supply chain crisis following both the COVID-19 crisis and the War on Ukraine highlighted this issue to many – if certain materials are unavailable, work may have to be redone.
Client-Related Causes of Construction Rework
- Lack of funding – Sometimes causes of rework are far outside of a contractor’s power, such as a clients’ budget either being reduced or running out in the middle of a project, which can lead to revisions.
- Poor client communication – A client may not share the right information with the right people, or fail to coordinate with a contractor. Such miscommunications will often lead to rework.
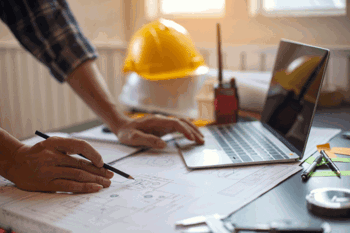
6 Ways To Reduce Rework In Construction Projects
Reducing rework may seem like a tough task when reviewing the wide range of causes that leads to costly rework, but there are plenty of approaches and processes which can help tackle the problems which lead to rework within a construction project.
The following solutions cover a wide range of factors, but the main key is strong coordination throughout a project from start to finish to help avoid missteps and tackling the systemic issues which lead to rework.
1. Connect Your Team Through A Digital Solution
Investing in technology which connects and coordinates team members can immediately tackle the overarching issues of miscommunication and poor coordination which leads to the majority of rework. It can take some time to choose and implement the technology which will be most effective for your business, but the effort involved at the top of a technology procurement project will lead to a significant reduction in rework required.
Construction-specific tools, such as an ERP system or a project management tool developed for the industry, will help you tackle and simplify the complicated processes involved in construction.
Software helps in countless ways, but the leading positive is providing a single source of the truth where every team member can gather information, review data, share communications and coordinate.
Any changes made throughout the project, including budget or project scope changes, will come through on the software in real-time and the adjustments needed to avoid rework are often automated.
While spreadsheets and emails have helped speed up and transform construction processes, connected digital solutions such as ERP software are the next step forward, where everyone has the right information at the right time.
Going digital and moving planning, coordination and project control to a powerful digital solution is one of the fastest ways to significantly minimise rework.
Reduce rework with Access Coins ERP
Access Coins is a powerful ERP system built for construction. Packed with features designed to meet the challenges of construction, Coins provides the ‘single source of truth’ needed to avoid miscommunications which lead to rework.
2. Collaborate In The Design Phase
A significant amount of rework happens due to mistakes made in the design phase of a construction scheme.
However, design teams and contractors will often work in silos. An approach called integrated design is essential to ensure these mistakes are spotted or minimised during the design and plan review process. ‘Design creep’ can be managed effectively to avoid rework during the construction phase.
If possible, for example when working to a design-build contract, design teams should work collaboratively with construction companies and bridge the gap between design and early-phase construction tasks such as estimating and procurement.
Sharing data between teams and keeping transparent communication can lead to stronger designs with fewer snags. This is also easier to do with a connected ERP system in place.
3. Take Advantage of BIM
Another way to tackle issues in the design process is to use Building Information Modelling (BIM) software to quickly spot and correct design errors before they are used in the final version of a building plan.
BIM software is a way to visualise building designs, allowing design teams to view and collaborate designs in real-time.
This level of visibility means aspects of the design which may clash with others, contain errors, or simply not look ‘quite right’ will be flagged by the software.
The software also has the power to combine data sets from multiple stakeholders to ensure everyone is in the right place. Architects, contractors and engineers can work collaboratively on a single model and ensure everyone is on the same page.
4. Budget More Time & Money In Preconstruction Phase
Investing more in the preconstruction and planning phases of a construction scheme should save your team time and money in rework during the construction phase.
Accurate estimates, good-quality data and strong document management are all essential to ensuring a reduced amount of rework and projects sticking to deadline and budget.
All project stakeholders should be involved in the essential preconstruction phase in order to ensure clear communication and strong planning to cut out any future bottlenecks. In this phase, any ambiguous plans, contradictions or missing elements can be spotted and corrected.
This is also the part of the project where schedules and sequences are set. Out-of-sequence work is a leading cause of rework, and spending time on setting out a well-planned and coordinated schedule will prevent issues which lead to rework further down the line.
Teams should also incorporate a ‘constructability review’ to help determine the real-world success of a construction project based on the current specifications, location and conditions.
Incorporating specialist software is a consideration to manage preconstruction processes.
5. Prequalify Your Subcontractors
Poorly-chosen subcontractors leads to poor work which will eventually have to be deconstructed as part of rework. As the labour shortage impacts the industry, it is vital to build excellent relationships with your subcontractor and specialist contractor network.
However, a simple way of finding great subcontractors and making the right hires is to send out prequalification questionnaires during the bidding and tendering process to help qualify subcontractors before they send out a bid.
Your questionnaire should ask subcontractors if they have the skills, equipment, resources and availability to work on your construction project. This will help you minimise risk of rework early on in your project, ensuring you get the best people for the job on-site.
6. Set A High Standard Of Field Communication
Miscommunication is another leading cause of rework which can be solved using technology.
Field communications can be hampered by multiple teams using multiple methods to keep each other updated (such as long and messy email chains or even sporadic group chats).
Project managers should introduce a single shared line of communication to help avoid those roadblocks that come from poor field comms. A communication plan outlining which channels should be used by which team members should be shared at the start of a project.
Cloud-based technology that provides every team member with the same view of the progress of a project, and a platform where they can easily communicate will gives teams confidence to coordinate and work in a way which will prevent the mistakes that lead to rework.
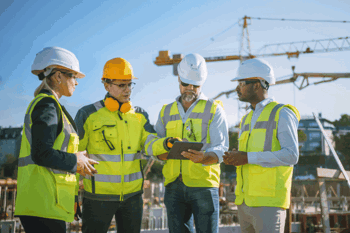
How To Handle On-Site Communication In Construction
- Ensure your subcontractors don’t work in isolation which leads to misalignment
- Project managers need to focus on key communications being shared to every aspect of a project, including subcontractors, suppliers, clients and inspectors
- Form and share a communication plan with clear instructions on how and when to communicate with other team members at the start of a project
- Use cloud-based technology, preferably with mobile access, to keep everyone informed within a single platform
- Incorporate daily reports into your communication plan
1. Regularly Check Quality Standards
Establishing a quality control process in a construction project is an important way to help reduce the amount of rework required in your build. This needs to be systemic across your build, ensuring every piece of work is checked to ensure quality assurance standards are met. While time-consuming, it is essential that quality control is in place across your project to avoid rework. All quality checks need to be documented and communicated across the team and to the client. This will also help increase the safety of your construction site, as any defects will be spotted and corrected quickly before posing any danger.
Technology can also be used to ensure quality standards are met, including software where workers can send in photos and videos of their work to be both recorded and inspected off-site by quality experts.
2. Invest In People
A longer-term approach to reducing rework is introducing a learning and development culture within your team. A 2009 study by the University of Gaza reported that contractors that regularly invest in training can reduce rework costs between 11-22%.
Those workers who are engaged in regular training to help develop their skills will produce better work.
With the current labour and skills gap affecting the entire sector, it is important to upskill employees through training, which in turn also helps with worker retention. This initial investment will pay off with savings on rework and an improved standard of work.
Your people are the most important part of any project, and reserving budget and time to help improve their skills and knowledge will strengthen your team, your professional reputation and result in cost savings.
3. Training For Construction Workers To Reduce Rework Could Include –
- Courses on new technology and materials used in construction
- Sessions on practical methods in construction to help upskill current workers
- A mentoring/buddy session where new workers are paired with experienced employees to learn on the job
- Health and safety training courses
- Training for construction managers
Reducing Rework In Construction As An Ongoing Process
Rework leads to more than lost profits – it can damage relationships, decrease morale and set projects off-course, but it does not need to be an inevitability in construction projects.
While there are very few ‘quick fixes’ to the problem, improving aspects of processes, culture and technology used will lead to the reward of reduced rework costs and impacts.
The guidance above will help your construction company develop those processes which tackle the main causes of rework – poor planning, miscommunication and design errors. These changes need to be made from the top-down and communicated effectively to make their desired impact.
It is also important to see reducing rework as an ongoing process, utilising new technology and regularly reviewing processes, alongside tracking the amount of rework required to determine the real impacts of these changes. The right approach will mitigate the need for rework and the costly impacts involved.
