What are the Biggest Issues in the Australian Construction Industry? – and how to Tackle Them
High interest rates, an ongoing housing crisis and lingering post-pandemic impacts are delaying the stabilisation of the Australian construction industry which continues to face an intense period of market challenges.
The construction industry is a mainstay of the Australian economy. It accounts for more than 10 per cent of GDP, employs around 1.35 million people and turns over $384 billion, making it one of the largest sectors in the country.
While positive sentiment is starting to emerge, let’s look at the current key challenges the industry is contending with and how to approach them.
What are the main issues in Australian construction industry?
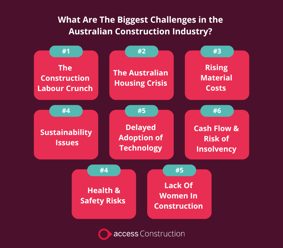
1.The labour crunch in construction
Many of the industry’s challenges today seem to stem from the labour shortage in construction. With highly fluctuating labour costs, project delays and supply chain instability, the skill shortage is arguably the biggest challenge facing construction.
As recently reported by the ABC, Buildskills Australia identified a workforce of an additional 90,000 people is required to meet the federal government’s goal of building 1.2 million new homes in the next five years. This competes with a booming infrastructure pipeline vying for the same labour.
The huge gap between labour availability and demand is rapidly growing.
Master Builders Australia executive Denita Wawn told The Australian Financial Review, while the construction industry employs a 1.35 million workers, it also contends with an annual exit rate of 8 per cent and only half of those people are being replaced each year.
The federal government's 2024-2025 budget announced $90.6 million to increase skilled construction workers. This includes a Fee-Free TAFE program and streamlining the migrant skills assessments process. While the industry welcomes the additional funding, the question of whether it will have enough impact to meet short term requirements remains.
With an evolving industry, ageing workforce, and low female participation, the challenges are there but construction companies can take steps themselves to try and mitigate the long-term effects of the labour crunch.
By focusing and investing in skills development for current employees, seeking out and mentoring students and graduates or offering apprenticeship programs may also encourage younger talent to show interest in the industry once more.
Showing progression in the adoption of technology, sustainability, diversity and work-life balance will also go a long way in making construction more desirable for this more conscientious generation. All this will help the next generation of workers to overcome their stigmatised view on construction.
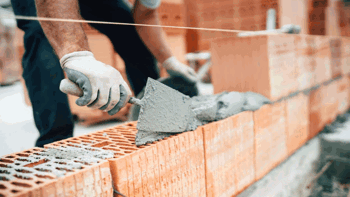
2. The Australian Housing Crisis
One of the biggest headlines in the news cycle is the Australian housing crisis.
The inability to meet the demand of Australia’s population growth has seen an extraordinary lack of supply of housing. Increased interest rates, supply chain shortages and higher building costs, meaning it’s extremely difficult for developers and construction companies to make a profit - often resulting in project delays, or in worst cases, businesses folding, and projects abandoned.
With a supply shortage and high costs of living, rental prices have skyrocketed and for many, buying a home is a fast-fading dream.
In addition to boosting skilled workers, Westpac chief economist Luci Ellis recently called for the need to improve productivity in the construction industry by internal innovation, as reported on realestate.com.au.
According to Master Builders Australia, productivity within the construction sector has declined 6.8% over the five-year period to 2022-23, however, as highlighted on realestate.com.au, investment in technology and adopting processes such as modular construction, are ways construction companies can improve efficiencies and reduce project costs.

3.Rising material costs
Material costs have long been a main concern in the Australian construction industry, impacting project budgets, timelines, and overall profitability. In 2024, this challenge has been exacerbated by various factors, ranging from supply chain disruptions to global economic shifts.
And the implications for businesses have been hard felt. The Australian Securities and Investments Commission (ASIC) reported a 42 per cent surge in insolvencies in construction, from 1,793 cases in 2022 to 2,546 in 2023 as reported on Build Australia, and the BCI Construction Outlook listed a surge in deferral rates as a key risk for the construction industry in 2024, due to rising construction costs and labour shortages.
Understanding the Factors Driving Material Cost Increases
- Supply Chain Disruptions: The COVID-19 pandemic highlighted vulnerabilities in global supply chains, causing disruptions in the availability and delivery of construction materials. Although many economies are on the path to recovery, these disruptions have persisted, contributing to ongoing material shortages and increased costs.
- Increased Demand: As economies rebound and infrastructure projects resume, the demand for construction materials has surged. This heightened demand, coupled with limited supply, has led to bidding wars and price escalations, further driving up material costs.
- Inflationary Pressures: Inflationary trends, influenced by monetary policies, geopolitical tensions, and other macroeconomic factors, have also played a role in pushing up material prices. Rising energy costs, for example, can directly impact the production and transportation expenses associated with construction materials.
Strategies for Tackling Rising Material Costs
- Strategic Sourcing: Construction companies are increasingly diversifying their supplier base and exploring alternative sourcing options to mitigate the risk of material shortages and price volatility. Establishing long-term relationships with reliable suppliers and leveraging technology for real-time supply chain visibility can help in this regard.
- Value Engineering: Adopting value engineering principles involves optimising project designs and specifications to achieve cost savings without compromising quality or performance. By reevaluating material choices, construction methods, and design elements, stakeholders can identify opportunities to reduce overall material costs while maintaining project integrity.
- Investing in Technology: Embracing digital tools and construction technology can enhance efficiency and productivity throughout the project lifecycle. Advanced project management software, Building Information Modelling (BIM), and procurement platforms can streamline workflows, optimise resource allocation, and facilitate better decision-making, ultimately mitigating the impact of rising material costs.
- Contractual Flexibility: Incorporating clauses and provisions in construction contracts to address price fluctuations and supply chain disruptions can provide a degree of financial protection for project stakeholders. Negotiating flexible payment terms, establishing escalation clauses tied to material indices, and incorporating contingency plans for alternative material sourcing can help mitigate risks associated with volatile material markets.
Future-Proof Your Construction Business With Access Coins ERP
Access Coins is an ERP system designed to tackle major issues within the construction industry, from tracking cash flow, procurement, increasing employee retention with HR and Payroll tools and providing visibility across large, complex projects.
4.The Need For Sustainability
The construction sector is under mounting pressure to embrace environmentally friendly practices, driven by evolving environmental regulations and shifting consumer preferences. Projects are not only being scrutinised for their financial viability, but for their carbon footprint.
According to the United Nations Environment Program (UNEP), the construction industry is the leading contributor to greenhouse gas emissions, responsible for almost 37% of total emissions. With these results aligning with global initiatives such as the International Energy Agency’s Net Zero Emissions by 2050 Scenario.
In Australia, Infrastructure Net Zero states infrastructure directly or indirectly contributes up to 70% of Australia’s carbon emissions, with the organisation setting an objective to decarbonise the country’s infrastructure to at least meet national targets of 43 per cent by 2030 and Net Zero by 2050.
Today, businesses are adopting and enhancing more efficient processes and methods to build, demolish and deconstruct their infrastructure. According to UNEP, investments in building energy efficiency amounted to USD $237 billion between 2020 and 2021.
Additionally, major businesses are now exploring further strategies, including the electrification of their vehicles, the utilisation of renewable energy sources like wind and solar, and transitioning to paperless operations.
The demand for more sustainable materials has already seen an increase and this is forecast to continue. However, a push for net zero in the industry is not all bad. Younger generations show a keen interest in sustainability which could help with labour shortages and presents an opportunity to plug the skills shortage gap.
5. Delayed Technology Adoption in Construction
The construction industry is notoriously hesitant to adopt new methods and technologies. This often comes down to businesses not having the time or budget to teach staff new ways of working.
The McKinsey Globe Institute named construction the second least digitised sector in the world.
Using multiple disconnected systems to manage projects is a major issue with slow technology adoption.
Managing numerous systems across an organisation and entering data several times is a laborious administrative task, prone to error and often results in guessing numbers and never knowing if information is correct.
Moving to a core construction ERP system to manage project control and financials standardises data and gives an accurate view of each project and a business as a whole. It also allows for in-depth analysis, improved forecasting and better decision-making, let alone connecting teams and improving collaboration.
While digitalisation within the construction industry appears to be gaining momentum, there remains ample opportunity for enhancement.
6.Cash Flow and Risk of Insolvency
Cash flow remains a volatile problem for the construction sector. As reported on ABC, fixed price contracts and subsequent rises in supply costs is a major challenge in the industry which can lead to cash flow issues.
A steady cash flow is crucial for construction. Your suppliers want to be paid after they have completed their work and do not care if your client has not paid. Having free cash to be able to pay subcontractors and suppliers before the project completion is necessary to avoid disputes, delays and damage to your reputation.
Company owners are often not trained in managing finances and do not have a background in accounting. Financial skills are learnt on the job, and so fund management is a common issue amongst construction firms. Combined with forgetful clients or unreliable subcontractors, a steady cash flow becomes an arduous task.
Unfortunately, 11.6 per cent of small construction businesses have payments owing to them that are more than 60 days overdue , significantly heightening the risk of encountering cash flow deficits. CreditorWatch data reveals 23.8 per cent of firms with an outstanding ATO debt of more than $100,000 are in the construction industry.
Encouragingly, legislation is being rolled out to help to protect subcontractor payments. The Queensland government has enacted a groundbreaking trust account framework designed to safeguard subcontractors’ payments even in cases of builder insolvency. Project Trust Accounts require project owners to deposit funds and progress payments into dedicated bank accounts from which a head contractor pays subcontractors. Only when all subcontractors are paid can the head contractor pay themselves.
Construction companies can tackle the cash flow problem by building a strong business credit profile. There are practical steps to achieve this:
- Ensure you have the right knowledge, systems and professional advice to manage building and construction finances
- Make sure paperwork and contracts are all in order with necessary signatures.
- If a client requests a change mid-project, make sure you have written signed agreements that can be referred to.
- Choose reliable subcontractors by asking suppliers or subcontractors you regularly work with to give recommendations.
- Check licenses and insurance before finalising a hire.
- Take every opportunity to build networks and upskill employees.
Overall, a healthy cash flow comes down to doing your research and surrounding the business with people you trust.
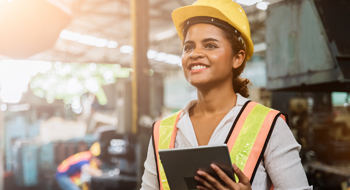
7. Health and Safety Risks
The construction industry made up 14 per cent of worker fatalities in Australia in 2022 and had the second highest number of serious claims.
Despite health and safety initiatives, the nature of the work in the industry implies a significant possibility of an injury happening sooner or later.
Accidents cause lawsuits and higher insurance premiums, which have a negative impact on a brand reputation and cash flow. Injuries also mean that you will have less available employees, which can be detrimental given the current skills shortage.
Failing to keep on top of health and safety compliance - such as onsite training, equipment compliance and accreditations - can result in fines as well as putting employees at higher risk. One of the main reasons for injuries is poor health and safety training.
The problem is that the majority of on-site construction injuries occur randomly, posing challenges in predicting and pre-emptively addressing them. Therefore, to effectively address this issue, it's imperative to cultivate a safety-centric mindset towards on-site operations. This entails allocating resources towards enhanced protective gear, comprehensive safety training initiatives, and the implementation of proactive safety protocols and software to respond swiftly to potential hazards.
8. The Need For More Women In Construction
The lack of women in construction is a pervasive issue. Despite career opportunities in the industry, many women are put off by its 'macho' stereotype of physical and messy work.
One way of breaking the stigma that 'construction is a man’s job' is through the tone of voice, language and imagery used in recruitment processes. Finding recruitment agencies that can offer advice on diversifying role descriptions in job adverts will help attract a wider pool of talent.
Amid labour crunches such as the ones the industry faces today, marketing the sector to a more diverse audience is a surefire way of overcoming skill gaps.
Although the industry is advancing towards greater inclusion, there remains room for improvement. In Australia, only 12.7 per cent of the construction workforce and 2 per cent of workers in construction trades are female.
The opportunity is there. However, the onus is now on companies within construction to seek out and adopt a more diverse approach to recruitment and onboarding, and this includes addressing work-life balance.
As reported in The Australian Financial Review, a recent survey of infrastructure trainees, including both female and male participants, indicated long working hours are a deterrent to a career in construction.
This issue also calls for businesses to evaluate their current employees to determine how well they are integrating their more diverse hires into the business. By focusing on fostering an environment that both men and women feel comfortable in, whether that is reviewing current company policies or even offering current employees diversity training.