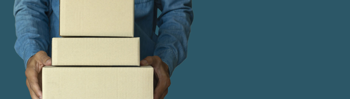
What is picking and packing?
Picking and packing is the process of selecting and packaging products in a warehouse. This includes ‘picking’ the right type and number of products from inventory and ‘packing’ them for shipment. Pick and pack is often the most costly and time-consuming process found in a typical warehouse.
For a pick and pack system to be effective, warehouse operations must be tightly organised and pick packer errors must be reduced to a minimum. To support warehouse staff, modern warehouses will often utilise automation and different warehouse technologies that increase efficiency.
Why is pick and pack process efficiency important?
There is a growing demand for rapid online shopping, which includes same-day delivery, with the ability to place an order at any hour, alongside the flexibility to cancel or change a delivery. The unpredictable nature of customer orders means that warehouses need to be efficient, flexible and responsive during their pick and pack process to reduce order completion time and keep customers happy.
Picking and packing is also time and cost-intensive, where some articles have even reported that picking accounts for as much as 60-70% of warehousing costs, up from the previously reported 55%. By streamlining the pick and pack process, warehouses can benefit from significantly reduced costs and mispicks, which is crucial when trying to keep up with competitors.
What is the pick and pack process?
1. Receiving
The pick and pack process starts when a customer places an order. The order information is sent from the ecommerce platform to the warehouse management system, and a digital or physical packing slip is generated.
2. Picking
A warehouse picker will then pick the correct items from the warehouse shelves using the packing slip. Picking is the most time-intensive part of the process and efficiency here is absolutely crucial for warehouse management. Different warehouses will use different picking methods, depending on inventory storage, order volume and other factors.
3. Packing
The order will then be packed into a suitable container for shipping, such as a box or bag. At this stage, orders should be verified to ensure they are correct, and packaging should be checked for damage. A shipping label will be printed and added to the box.
4. Shipping
Finally, the package is then prepared for shipping and organised, ready for collection from the carriers.
Different pick and pack methods
The type of warehouse picking and packing method you use will depend on the products you are storing, sales volume for the business, and the amount of space you have available. For most warehouses, it will likely fall under one of these 4 methods:
1. Piece Picking
Piece picking is the process of picking, packing and shipping one singular order at a time. It’s very simple, so it’s perfect for small retailers who are just starting out. As it’s heavily time-intensive, larger retailers, or those looking to scale, should opt for a more complex method.
2. Batch Picking
Batch picking, or multi-order picking, is the process of picking multiple orders at once. This method is ideal for businesses who are starting to experience a higher volume of orders and need to save time in the picking process.
3PLs and warehouse operators should be starting to consider software solutions that can help teams manage the process effectively.
3. Zone Picking
Zone picking is a method where warehouse pickers only pick items from a specific zone they are assigned to. A packing slip will move through multiple zones, where the order is gradually picked until it is complete and ready to be passed over to the packing station.
This method is most suitable for retailers who ship a high volume of orders. With the complexities of zone picking, warehouse management software is recommended to avoid costly mistakes and help pickers manage orders efficiently.
4. Wave Picking
Wave picking, or cluster picking, is the method of picking multiple orders across different zones at the same time. Usually coordinated by warehouse management software, the system will identify similar clusters of orders and release them at the same time for picking. Warehouse pickers will then work in their zones to pick the correct items, before consolidating the orders at the packing station.
Due to the complexity and organisation required for wave picking, this method is best for large retailers with a high volume of orders, supported by warehouse management software.
Warehouse picking and packing best practice
Below we’ve listed four tried and tested solutions that will help improve the picking and packing process for any retailer, 3PL, or warehouse operator:
1. Plan picking routes to save time
Research has shown that travelling during the picking process takes up 55% of the complete order-picking time. To reduce order completion time, warehouses need to plan out the most efficient picking routes possible.
When planning a picking route, take into consideration:
-
The size of the warehouse will dictate the number of picking routes required.
-
The layout of the warehouse will dictate the most efficient route for the pickers to take.
-
The type of products being stored in the warehouse will dictate the order in which the products are picked.
The volume of goods being stored in the warehouse will dictate the number of products that need to be picked per route.
2. Choose an effective inventory storage strategy
To improve picking and packing speed, make sure to consider how you are storing inventory across the warehouse.
Consider options such as volume inventory management, where products with the highest turnover are stored nearest to the packing station. The more popular the product, the quicker a picker can reach the stock, helping to reduce time spent picking.
An inventory management system is often used by warehouses to help further improve the picking and packing workflow.
3. Use barcode scanning to avoid errors
Picking is a labour-intensive process which can often result in mispicks, leading to costly errors and unhappy customers.
Mobile barcode scanning significantly improves picking accuracy, helping to reduce errors and costly mistakes. Barcode scanning software can also help suggest optimal picking routes for each individual warehouse worker.
This is an example of automated warehouse technology which is becoming increasingly common amongst modern warehouses. Warehouses need to consider investing in barcode scanning, otherwise it’s likely they will be left behind when competitors offer faster and more efficient order fulfillment services.
4. Increase efficiency with a warehouse management system
For a warehouse to perform at its best, a warehouse management system (WMS) is strongly recommended. By using cloud-based warehouse management software, warehouses can benefit from automated workflows, optimised stock control and advanced location management.
With these features in place, the picking and packing process can be supported by automation and streamlined workflows. A WMS can also help warehouses as they grow and scale, ensuring a growing volume of sales and increasingly complex orders are processed with ease.
The future of picking and packing
As technology evolves and automation continues to improve warehouse operations, warehouses will need to turn to advanced methods to ensure their picking and packing process is as efficient as possible. This is especially true when giants, such as Amazon, are constantly finding ways to speed up order completion.
From mobile barcode scanning to cloud-based warehouse management software, Mintsoft offers a range of logistics software solutions to ensure you are meeting, and exceeding, best practice.
To transform your warehouse picking and packing, learn more about our warehouse management software or view our 4 minute demo today.
Frequently asked questions
What is warehouse packing? |
Warehouse picking is a process that involves locating and gathering items from a warehouse. This can be done manually or with the help of automated systems. |
What is a picking list? |
A picking list is the piece of information that is sent to warehouse pickers after a customer has made an order. It will include a list of products and items which need to be picked, the location of these products, the picking route and the shipping data. |
What is warehouse packing? |
Warehouse packing is the process of packing the items of an order after they have been picked. Warehouse packers need to select the correct packaging, weigh the materials and ensure the package is labelled with the correct shipping label. |
How can you improve picking and packing? |
Ultimately, to improve the picking and packing process, you should:
|
What are the three main picking systems? |
The three main picking systems include batch picking, zone picking and wave picking. Depending on their requirements, warehouses may use a combination of one or more of these systems |