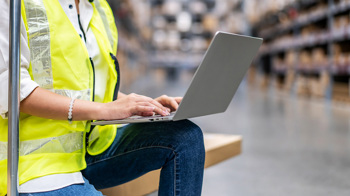
The challenges of a growing fulfilment industry
With Australians increasingly embracing online shopping, retailers and 3PLs have a massive opportunity to service this demand and grow their businesses. But with this opportunity also comes challenges.
Globally and locally, the fulfilment landscape is increasingly competitive. The low barrier to entry means that practically anyone can purchase stock and open an online store in no significant amount of time. There is also, of course, the ever-burgeoning presence of established global names like Amazon to contend with.
Add to this the fact that online customers are increasingly expecting near-immediate deliveries, and you have a situation where any advantage retailers or 3PLs can gain is critical to stay ahead of the competition.
Gaining an edge in an increasingly competitive industry
Like any retailer or 3PL, achieving your revenue goals and minimising expenses is critical. So too is boosting your productivity and ensuring that you are constantly increasing the return on any investment.
But how can you improve productivity if you do not have the means to accurately track and measure it? Having visibility of your end-to-end fulfilment process, with the ability to track and measure the effect of changes – whether improvements you have implemented, or those created by external forces – is key.
This visibility starts in the warehouse. Knowing the cost of different tasks performed by warehouse staff, and the time it takes for them to do so, allows you to measure just how productive they are for each dollar spent.
How you can easily track and improve productivity
In decades past, measuring the productivity of your warehouse was both time-consuming and inaccurate. Understanding how long it took to pick and pack an order, or to receive some stock, would require watching the process in person, armed with a stopwatch. Today, things are far simpler.
With warehouse management software like Access Mintsoft, you can digitalise the tasks performed by your warehouse staff and gain real-time insights into their productivity via the solution’s advanced data analytics.
Software not only gives you the visibility to measure staff performance, but also boost their productivity. For instance, it removes the need for staff to print off pick lists. Instead, they can much more easily pick products by using a mobile scanner.
Once you embrace digitalisation offered by software, the productivity gains only increase. Powerful automation capabilities mean that you can eliminate countless time-intensive, error prone tasks that have been holding productivity back for years.
For instance, warehouse management software can enable you to automate anything from producing shipping labels, to tracking orders and creating commercial documents. Warehouse staff can save massive amounts of time and you can minimise costly errors that not only harm your bottom line, but customer loyalty too.
Optimising your processes and warehouse
The benefits of a warehouse management system do not end with simply automating tasks and tracking productivity. It helps you make the most of your staff and warehouse, to get more value from each dollar spent.
This is where data analytics come in. Instead of manually sifting through mountains of data to work out how many staff you require for the day, or the minimum amount of inventory you need, warehouse management software can do that for you. It can even automatically reorder stock when levels get low or notify staff when shifts are available.
Software can also deliver productivity gains simply by making work easier for your staff. For instance, it can improve picking and packing efficiency by providing a graphic layout of your warehouse, allowing staff to easily see where items are picked from the most. Chat interfaces (with automatic translation capabilities) can also make communicating and sharing information quick and simple.