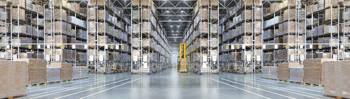
Ecommerce warehouses explained
So, what is an e-commerce warehouse exactly? In essence, it is a facility where inventory is stored and managed to cater to the demands of online retail operations. Stock is received at the warehouse and stored appropriately within, and when a customer places an order online, it is picked by warehouse staff, packaged, and delivered via courier to their doorstep.
Not all e-commerce businesses use a warehouse, especially in their early days. A garage or spare bedroom may suffice when order volumes are low, but as they grow, a warehouse is increasingly needed to ensure enough stock to fulfil all orders. Smaller online retailers at this stage of growth may use a warehouse managed by a third-party logistics (3PL) provider.
What does ecommerce warehousing involve?
With the constant movement of stock in and out of the warehouse, the staff who make it all happen, and the supply chain processes they follow, modern ecommerce warehouse management is often a complex undertaking. It goes beyond merely ordering stock and storing it in the warehouse, encompassing a range of considerations, including:
-
Stock receiving: Ensuring protocols are in place so goods are received in the most efficient way possible, regardless of the time of day.
-
Storage: Placing stock in the warehouse so staff can easily access items to be processed for orders.
-
Optimising space: Organising the warehousing so staff can pick and pack orders efficiently, ensuring they have sufficient space, and minimising the distance they must travel to retrieve items.
-
Stock control: Managing inventory to ensure the right amount of stock is on hand to fulfil every order, as well as identifying in-demand items and anticipating future demand.
-
Processing returns: A system must be in place to inspect returned items to determine if scrapping is necessary and, if so, to order replacement stock.
-
Warehouse staff: Ensure health and safety measures are in place and all staff are sufficiently trained and managed to ensure optimal use.
-
Equipment: Tracking all equipment used in the warehouse to handle stock, from pallet jacks and tote bins to more complex machinery like Autonomous Mobile Robots or robotic arms.
What types of ecommerce warehouses are there?
Fulfillment centre: A fulfillment centre is a warehouse location designed specifically to enable order fulfillment services, rather than the storage of stock. While stock is held in traditional warehousing for longer periods of time, often months or years, a fulfilment centre holds stock in the shorter term. Specifically, for the period between when a customer places an order and when it is shipped to their address.
While a traditional warehouse is designed to maximise storage space, a fulfilment centre focuses on moving and processing stock as efficiently as possible.
Distribution centre: A distribution centre serves as a hub for managing inventory that is to be transported to another location, holding stock for a short period of time. As opposed to a fulfilment centre, which is used to store and then send stock to customers, a distribution centre is used to store and send stock to a retailer or wholesaler.
Leased warehouse: This is a rented storage facility used by ecommerce businesses to store inventory. Unlike purchasing a warehouse outright, leasing offers cost savings and flexibility, with maintenance and repairs typically handled by the landlord.
Dropshipping centre: This facility is used by a product's manufacturer to store items and ship them directly to the customer, without the need for an ecommerce business to hold inventory.
Automated warehouse: An automated smart warehouse is a facility where storage, retrieval, and movement of goods are primarily performed by automated systems, reducing the need for manual labour. These systems can include robots, conveyor systems, and automated storage and retrieval systems (AS/RS). This type of warehouse is typically used for fast-moving smaller items that require only short-term storage.
3PL warehouse: This warehouse space is operated by a 3PL that offers services such as warehousing, inventory management and order fulfillment for ecommerce businesses. Outsourcing these functions can provide flexibility and cost savings for businesses.
Consolidated warehouse: This is a facility that consolidates goods from multiple sources or suppliers into a single location for storage and distribution. It removes the need for each supplier to maintain its own separate warehouse, which can lead to reduced costs and increased efficiency with inventory management and logistics.
Regional warehouse: Regional warehouses are strategically located closer to target markets or population centers to reduce shipping times and costs. They help ecommerce businesses reach customers more quickly and efficiently.
On-demand warehouse: This is a storage facility that offers flexible and temporary storage solutions based on businesses' specific needs. Unlike traditional warehouse operations that require long-term contracts or leases, on-demand warehouses can be rented for short periods. They cater to businesses with fluctuating inventory levels, seasonal demands, or short-term storage needs.
Temperature-controlled warehouse: This form of warehouse is equipped with temperature control systems to store products that require specific temperature conditions, such as perishable goods or pharmaceuticals. Its temperature and humidity are kept at a constant level to ensure the stock remains in good condition.
5 tips to enhance ecommerce warehousing efficiency
1. Integrate your ecommerce systems
Logging into and manually tracking disparate marketplace, shopping cart and courier platforms, in addition to performing data entry to ensure sales and inventory data are in sync, is one of the biggest (and unnecessary) burdens placed on e-commerce businesses.
The right warehouse management software can help you integrate all these disparate platforms into one solution, allowing for data to be synchronised across all and removing the need for manual data entry. This means that sales data from multiple channels are always in sync with inventory data, and you can easily track incoming orders and their progress in one dashboard.
By integrating courier platforms, the system can automatically select the most timely and cost-efficient courier for each order, based on rules you define. A warehouse management system can also offer integration with other core business platforms like a CRM, accounting software or ERP solution, allowing for seamless data transfer and synchronisation.
All this consolidation will save you countless hours of frustration managing multiple platforms as you may do with other ecommerce software, make processing and tracking orders far more efficient, and ultimately help you get orders out faster.
2. Establish inventory thresholds
Ensuring you do not have too much, or too little stock is a delicate balancing act. Too much stock can mean incurring higher storage costs, not to mention facing the risk that items become damaged or out-of-date. Holding too little stock, on the other hand, can lead to unfulfilled orders.
That is why it is critical to establish minimum inventory thresholds for when you need to reorder stock. The most advanced warehouse management systems allow you to set these minimum thresholds, which, when hit, trigger the automatic reordering of stock. They can also enable you to forecast demand for certain products based on sales, seasonality, customer, and other data.
3. Enhance the pick and pack process
Picking and packing is one of, if not the most time-intensive aspects of order fulfilment, and a warehouse management system can help make it far more efficient and accurate. The software can enable you to identify the most efficient picking routes and store goods in the most optimal locations to boost picking and packing speed. For instance, it can automate workflows to ensure in-demand ecommerce products are stored nearest to the packing station.
The software can also coordinate more complex picking strategies, like zone picking or wave picking, which can help reduce the distance pickers need to travel to retrieve items. It can enable you to use barcode scanning and voice-assisted picking commands that significantly reduce picking errors.
4. Automating warehousing work
With the help of important warehouse technology, online businesses can automate many manual tasks that consume the time and effort of their warehouse staff. We mentioned earlier how software can automatically select the most cost-efficient couriers, but it can also automate the creation of pick lists and fast shipping labels.
A warehouse management system also facilitates customer communications by automatically sending emails, invoices, and order progress notifications. It also automatically updates users about an order's status.
The system also allows you to set rules to automatically determine what happens to orders during packing based on the delivery option selected, value, and weight. It can also automate the process of adding new items to inventory, tracking sales, and updating stock levels.
5. Implementing ecommerce warehouse management systems
Of course, all the benefits of ecommerce warehousing we have outlined so far are easily achieved with the help of a warehouse management system. Such solutions allow you to integrate all your disparate e-commerce platforms into one solution, eliminate manual warehouse processes and admin, and provide real-time visibility and control of inventory.
A warehouse management solution is specifically designed to help you remove unnecessary complexity and processes and spot areas for improvement. It provides advanced automation features that streamline everything from receiving and storing stock to picking, packing, and delivering orders, not to mention ensuring you have a bird's eye view of the entire fulfilment process.
Automate your warehouse with Access Mintsoft
If you are looking for a warehouse management system that offers all the capabilities outlined in this article and more, Access Mintsoft might be the answer.
Trusted by over 600 leading ecommerce businesses worldwide, the solution consolidates orders from multiple online ecommerce platforms, streamlines picking processes and eliminates countless manual tasks.
Access Mintsoft provides real-time visibility of inventory and order status so your team can prioritise picking and packing tasks based on urgency and demand. It also allows you to optimise picking routes and easily coordinate strategies like zone or wave picking.
Boasting 175+ pre-built integrations with major couriers and marketplaces, as well as API connectivity to integrate other platforms like accounting or ERP solutions, Access Mintsoft allows you to simplify all your critical business functions in one place.
Contact us today to book a demo or discuss how Access Mintsoft can help your business.
Watch Video: Top 4 ways Mintsoft can help automate your order and warehouse processes.