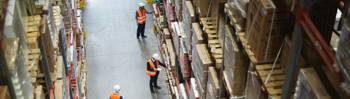
How technology can minimise errors in the picking process
Warehouses and fulfilment centres worldwide are increasingly turning to a range of innovative technologies to reduce errors and boost operational efficiency. Some of the most effective include:
Pick-to-light technology
LED lights are now being used for more than just their light-emitting quality. They are an essential component of pick-to-light and put-to-light technology. This innovation utilises LED lights on racks and shelves to indicate pick locations, making the task of finding items far simpler for warehouse staff.
All they have to do is scan the barcode on a shipping container, which illuminates the LED lights for listed items, making them easy to locate.
Autonomous mobile robots
Autonomous mobile robots (AMRs) help take human error out of the picking and packing equation. Not by replacing human packers, but by lessening their mental strain.
Warehouse automation robots reduce the amount of unnecessary walking required of human warehouse staff. They help guide them to picking locations via the shortest route possible, and not only that, provide critical instructions that can lessen mental load, like which products and quantities to pick.
The more that AMRs can help human warehouse staff, the less their physical and mental strain. And therefore, the better their picking error rate.
Warehouse management solutions
By automating time-consuming tasks and enhancing warehouse efficiency, like AMRs, warehouse management software can lessen the physical and mental strain placed on warehouse personnel.
These affordable and easy-to-use cloud warehouse automation solutions help them locate and store inventory as efficiently as possible. With just a few clicks, they can provide them with real-time visibility of accurate inventory information.
All this serves to reduce their workload and levels of fatigue and, therefore, common mispicking errors.
When was the last time you assessed your storage strategy?
Periodically reviewing your storage strategy and updating it with the latest best practices is key to minimising picking errors. In your next review, make sure to incorporate the following accuracy-boosting tips:
-
Repositioning fast-moving products to more accessible locations in warehouse.
-
Keeping frequently picked products close to designated packing and shipping areas.
-
Checking that all items are adequately labelled and placed in appropriate slots in the warehouse space.
-
Segregating different products/parts in different storage bins helps minimise the chance that incorrect items are selected.
-
Storing the same product in a single location thereby eliminates the errors and inefficiency that can arise from picking the same product from multiple locations.
The importance of correct identification and labelling
When you properly identify and label items, your picking error rate is going to decrease. It sounds simple, and with the right warehouse management system, it is. These solutions allow warehouse personnel to easily identify items by using a mobile barcode scanner.
Once they know what the item is, optimally placed signs, aisle designators, and shelf labels make it easy to know where to store it. To make this process possible, it is vital that all package sizes have a unique SKU and distinctive labelling.
Preventing errors with frequent inventory checks
A large proportion of picking errors stem from earlier mistakes. In particular, those made during replenishment or stock putaway, which often see items stored incorrectly or in the wrong location.
Periodic inventory checks are one of the safeguards against this happening. They are also vital for keeping tabs on stock levels. If you do not want to avoid understocking fast-moving products, or overstocking slow-moving ones, then regular inventory checks are vital.
Assign IDs to staff to spot errors fast
If you do not know which warehouse staff account for which errors, it will be hard to make improvements. That is why assigning a unique ID to each staff member – allowing you to identify where and by whom an error has occurred – is such an effective way to decrease picking error rates.
Armed with this knowledge, you can easily track the error rates of individual staff members and earmark those requiring further training. An ID system can also help warehouse managers see who is responsible for what, allowing them to monitor the progress of orders far more easily.
How Access Mintsoft can help minimise your warehouse picking errors
Picking errors, while rare for most warehouses, can wreak significant damage to customer satisfaction, and as a result, your bottom line. Warehouse management software like Access Mintsoft can not only help you reduce errors, but also boost pick and pack productivity and accuracy.
This powerful, easy-to-use cloud solution can help eliminate the manual tasks that place mental and physical strain on your warehouse staff. It can also help you optimise stock locations, product labelling and inventory tracking, so you and your staff can save previous time and work more effectively.
Book a demo or download a brochure of Access Mintsoft today to discover how you can save time, reduce errors and boost warehouse productivity.