How to Implement a Construction ERP System: The key steps and common challenges
In the fast-paced construction industry, implementing an ERP system has become crucial for ensuring project success and keeping a competitive edge.
By integrating all aspects of construction resource planning, an ERP system enhances efficiency, improves decision-making, and streamlines operations from project inception to completion.
This guide will explore the step-by-step process of implementation, how to avoid common issues and provides best-practice advice for ensuring your implementation goes as smoothly as possible.
What Is A Construction ERP System?
A construction ERP system is an integrated solution designed to manage and optimize all aspects of a construction business, from project planning and budgeting to procurement and resource management.
Tailored specifically for the construction industry, it ensures seamless collaboration and efficiency across all departments.
Learn more in our dedicated article: What is Construction ERP?
How Long Does It Take To Implement A Construction ERP System?
Implementing a construction ERP system typically takes between 6 to 12 months, depending on factors such as the complexity of the software, the size of your company, and the quality of your data. As every implementation is different, this is only a rough estimate.
Clear goals, thorough planning, and dedicated support internally and externally can help speed up the process.
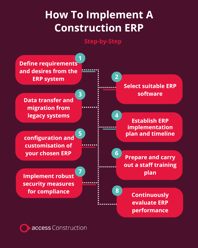
8 Key Steps To Setting Up An ERP System In Construction
Implementing a construction ERP system can be a complex process, but following a structured step-by-step approach helps ensure a smooth transition and minimises potential issues.
Construction technology experts recommend adhering to these essential steps, as they cover all critical aspects of the implementation process.
By following this guide, you can streamline setup, address potential challenges proactively, and fully leverage the benefits of your new ERP system.
1. Define requirements for the construction ERP system
Begin by identifying the specific needs of your construction business, such as project management, cost tracking, or procurement.
Engage with stakeholders to gather input on essential features and functionalities. Clearly documenting these requirements will guide your ERP selection process and ensure that the systems you shortlist will meet your business goals.
2. Select a suitable ERP solution
Choose an ERP software that aligns with your defined needs and industry requirements. Consider factors like scalability, ease of integration with existing systems, and vendor support.
There are many ERP systems on the market today, but only a few are purpose-built for construction. It’s highly recommended that you seek out a system that has been designed for construction’s project-based requirements.
Evaluate different options through demos and trials to ensure the software fits your business processes and operational needs.
3. Data transfer and migration from legacy systems
Next, you need to plan and execute the migration of data from your existing systems to the new ERP platform. This involves cleansing and validating your business’ existing data to ensure accuracy. Work closely with your ERP vendor to ensure a smooth transition and minimal disruption to ongoing operations.
- Assign A Data Officer: Designate a dedicated data officer or team responsible for overseeing this process. This person will ensure that data is accurately transferred and address any issues that arise.
- Gather All Data Sources: Compile a comprehensive list of all data sources and systems that need to be integrated into the new ERP. This could include databases, spreadsheets, etc.
- Cleanse and Validate Data: Before migration, clean and validate your existing data. This means checking for duplicates, errors, and outdated information to ensure that only accurate and relevant data is moved.
- Outsource Data Validation: Consider outsourcing the data validation process to specialized vendors if it’s time-consuming or complex. This can help ensure thorough and efficient data handling.
4. ERP Implementation plan and timeline
Together with your chosen ERP vendor, create a detailed implementation plan that outlines each phase of the ERP deployment, including milestones and deadlines.
This will likely be managed by a combination of both internal and external resource. Overseeing an implementation can be very time consuming, so it’s best to ensure that you have dedicated resource for the process.
Establish a timeline that factors in testing, configuration, and any potential blockers. Regularly review progress to stay on-track and address issues promptly.
5. ERP system configuration and customization
Many construction ERP systems are configurable, which allows your business to carve out purpose-built functionalities that work around your requirements and business processes.
On the other hand, most ERP vendors will offer module-based packages, from which you can select and choose the functions you need.
Discuss this with your vendor, as configurations may involve setting up workflows, defining user roles, and integrating with other tools.
6. Staff training
Provide comprehensive training for your staff to ensure they are comfortable using the new ERP system.
Some ERP vendors, including Access Coins, provide staff training as part of the onboarding process. In order to ensure your team is getting the most out of your new ERP system, it’s recommended you also arrange for comprehensive training to be carried out internally.
The training should cover key functionalities and best practices to maximize efficiency. Consider ongoing support and resources to help staff adapt to the system effectively.
7. Data security and compliance
Implement robust security measures to protect sensitive data and ensure compliance with industry regulations.
This includes setting up access controls, encryption, and regular audits. This is also the moment where you can address any compliance requirements specific to the construction industry. This will be far easier to achieve with a construction-specific ERP system.
8. Continuous evaluation and improvement
Post-implementation, continuously monitor the ERP system’s performance and gather feedback from your team. Regularly assess the system’s effectiveness and make necessary adjustments to improve functionality and address any emerging needs.
Some ERP vendors will assign an account manager who is your point of contact for arranging any changes or improvements to the system. Work together closely, as continuous improvement will help you maximize the benefits of your ERP investment.
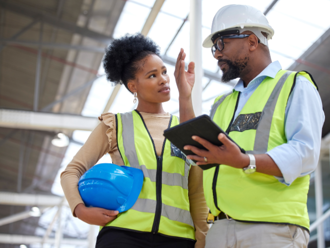
6 Common Challenges When Implementing a Construction ERP System
Implementing an ERP system in the construction industry presents several challenges. Being aware of these potential hurdles and having strategies to address them can significantly ease the transition.
1. Resistance to Change
Employees can often be resistant to adopting new technologies or processes.
Solution: Engage staff early in the process, highlight the benefits of the ERP system, and provide comprehensive training to ease the transition.
2. Data Migration Issues
Moving data from legacy systems can be complex and error prone.
Solution: Plan data migration carefully, conduct thorough testing, and consider working with experienced consultants to ensure data accuracy and integrity.
3. Customization and Integration
Ensuring the ERP system integrates well with existing tools and is customized to meet specific needs can be challenging.
Solution: Clearly define your requirements upfront, work closely with your ERP vendor, and allocate time and resources for customization and integration efforts.
4. Cost Overruns
Implementation costs can exceed initial estimates, impacting budgets. This can include anything from hidden costs to unforeseen issues.
Solution: Highlight any and all costs with your vendor early. Develop a detailed project plan with a clear budget and include contingency funds to cover unforeseen expenses.
5. Insufficient Training
Inadequate training can lead to underutilization of the ERP system and a general sense of unrest within your business.
Solution: Provide extensive training for all users throughout the implementation process and establish ongoing support to address any issues that arise post-implementation.
6. Lack of Dedicated Support
Without strong support from internal members of your team, the project may lack the necessary resources and commitment to oversee the implementation.
Solution: Ensure that you have dedicated members of the team responsible for overseeing and managing the implementation alongside your ERP’s account manager.
Access Coins is the all-in-one ERP built for construction
Designed specifically for the challenges of the construction industry, Access Coins’ integrated modules are built to manage the entire lifecycle of a construction project.
Implement a Construction ERP System with Access Coins
Implementing a construction ERP system is a crucial step towards enhancing efficiency and managing complex projects effectively.
Access Coins is a construction-first ERP system with a huge range of features and functionality developed to help construction businesses maximize efficiency and control costs.
- Collaborate, control and connect with Access Coins – control and track all aspects of the construction lifecycle from a single source of truth.
- Gain project and financial transparency through real-time centralised data.
- Expert implementation, with dedicated product training and customer support.
Explore our construction ERP software to find a solution that aligns with your business goals and optimizes your operations.
Want to find out more about Access Coins ERP?