What is a Submittal in Construction? Submittal Definition, Processes, and Types
A submittal in construction is the documented verification process where builders, estimators, and contractors confirm their planned materials and methods match project requirements.
Chief executives, project managers, and commercial directors in the construction industry face mounting pressure to keep construction projects on track while meeting exact design specifications.
Construction submittals center on preventing costly delays and errors through proper documentation. When materials or equipment don't match requirements, projects stall, costs spiral, and deadlines slip.
This article covers why submittals are so important in construction, submittal types, the submittals process and submittal best practices.
What is a Submittal in Construction?
In construction, a submittal is documentation that subcontractors provide to general contractors for design team approval.
Submittals in construction can include shop drawings, materials samples, specifications, installation guides, and quality control certificates that verify materials and installation methods match project specifications.
General contractors manage the submittals process, collecting documentation from subcontractors before sending to architects or engineers for review. Modern project management software helps CEOs, managers, and site teams track construction submittals through each stage—from initial documentation to final approval.
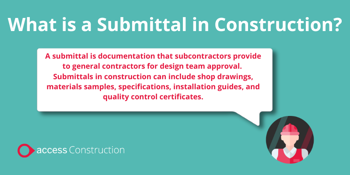
Submittals in Construction: Key Takeaways
- Submittals document project materials, specifications, and installation methods before construction starts
- Shop drawings, material samples, and product data make up most construction submittals
- Design teams review submittals to verify materials match project requirements
- Automated software streamlines submittal tracking, reviews, and approvals
- Clear submittal statuses prevent costly rework from unapproved installations
Why are Submittals Important in Construction?
Construction submittals prevent costly rework and schedule delays for project managers and site teams.
When architects review materials before installation, CEOs avoid profit losses from incorrect specifications, quantities, or installation methods.
Materials ordered without proper approval often require complete removal and replacement, causing budget overruns.
Project managers save time through proper submittal management, eliminating the need to remove and replace incorrect materials.
Directors maintain quality standards throughout construction while keeping projects within budget and on schedule.
Types of Construction Submittals
Construction submittals vary based on project requirements and contractor specialties. Project managers need different documentation formats throughout the construction timeline - from pre-construction planning to completion.
Common pre-construction submittals include:
- Shop drawings
- Material samples
- Engineering calculations
- Product data
- Mockups
Project closeout submittals include:
- Product warranties and manuals
- As-built drawings
Shop Drawings
Shop drawings show subcontractors' plans for manufacturing or installing specific project parts. They focus on prefabricated or custom-made components, allowing design teams to check whether products match project needs.
A typical example is electrical work. Electrical contractors create detailed layouts showing where outlets, circuits, and panels go. These drawings help teams confirm that everything meets building codes and project requirements.
Subcontractors submit shop drawings, including measurements, materials, and technical specifications. The design team reviews these details to ensure proper integration with other building systems and compliance with project standards.
Material Samples
Physical products give teams a real preview of what they'll work with. Paint swatches, flooring sections, and tile samples help match colors and textures accurately—something data sheets can't always show. Construction managers need these tangible examples to make informed decisions.
A paint chip shows true color under different lighting, soil samples demonstrate proper composition, and fabric swatches prove durability. Project designers can then verify if each material fits their planned aesthetic and quality standards.
Engineering Calculations
Mathematical proof validates a contractor's work meets engineering standards. Electrical contractors submit voltage drop calculations and load analyses to prove their systems can handle power demands.
The math behind construction projects prevents system failures. Load-bearing calculations show if structures can support intended weight, while electrical calculations prove systems won't overload. A structure’s power system needs precise calculations to guarantee uninterrupted service for equipment.
Product Data
Cut sheets provide detailed specs of construction materials and equipment. Subcontractors submit these technical documents to share product information with design teams.
A typical cut sheet includes:
- Product dimensions and specifications
- Installation instructions
- Required preparation work
- Performance ratings and data
- Warranty information
- Maintenance guidelines
HVAC contractors can submit fan cut sheets detailing airflow rates, power requirements, and installation steps. Design teams review these specifications to verify each product meets building codes and project requirements.
Mockups
Physical models showcase how components will look and function in real conditions. Window systems and lighting fixtures often need full-scale mockups to test their performance and appearance.
Contractors build these models using actual project materials and methods. Design teams inspect them for quality, fit, and finish. When mockups prove too large to move, contractors submit detailed photos or build sections directly on-site for review.
Large-scale mockups help teams spot potential issues before full installation begins. Suppose a window system mockup might reveal water infiltration problems or installation challenges. After approval, on-site mockups often become part of the final project.
Product Warranties and Manuals
Documentation outlines coverage terms for materials, equipment, and installed systems. Contractors submit warranty paperwork during construction, followed by executed warranties at project closeout.
Operating manuals accompany warranties to explain proper maintenance procedures. Fire alarm systems need detailed programming guides, while elevator installations require specific safety protocols.
Maintenance teams refer to these documents for equipment care, testing schedules, and troubleshooting steps throughout the system's lifespan. Complex installations like HVAC units or security systems come with detailed maintenance schedules.
Each manual includes step-by-step procedures for regular upkeep, emergency responses, and parts replacement. Project managers store these documents for future reference and training new maintenance staff.
As-Built Drawings
Final diagrams document the completed construction work with all approved changes. When contractors finish installations, they update the original shop drawings to show the exact locations of components and systems.
Design teams compare as-builts with initial plans to verify the proper implementation of changes.
MEP contractors mark relocated pipes, adjusted electrical routes, or modified ductwork on their drawings. Facility managers later use these accurate records for maintenance, repairs, and future modifications to the building.
Access Coins ERP – Developed by and for construction experts
Access Coins is an all-in-one ERP that covers everything from cost forecasting to workforce management.
What Information is Included in a Submittal?
Construction submittals need clear identification details and tracking information. Each package includes a transmittal cover sheet listing all included documents.
Standard submittal forms include:
- Project Name - Identifies which construction job the documents belong to
- Spec Section - Reference numbers that link to specific project requirements
- Submittal Number - A unique tracking ID for each document
- Revision Number - Tracks different versions as changes are made
- Package Number - Groups related submittals together
- Submittal Manager - Contact information for the document manager
- Submission Date - When the documents were sent
- Received Date - When the documents arrived
- Approver Details - Contact information for all reviewers
- Response Options - Standard responses like "Approved," "Approved with Notes," "Revised," or "Rejected"
- Notes Section - Space for feedback and revision requirements
General contractors and design teams add comments about changes or rejections in designated spaces. Subcontractors often bundle related submittals into packages with a single transmittal form, streamlining the review process.
Project managers track each submittal's progress through version numbers and status updates, ensuring smooth document flow between teams.
What is the Submittals Process?
Construction teams follow specific steps to review and approve project materials and specifications. Quality control requires proper timing—moving too fast leads to mistakes, while slow approvals cause project delays.
Project owners, architects, engineers, and contractors participate in the four-step review process:
1) Creating a Construction Submittals Schedule
General contractors map out timelines for each project submittal, marking deadlines and assigning responsibilities. Proper scheduling prioritizes materials with long delivery times ahead of finishing work components.
Project managers list every required submittal with expected review periods. A well-planned schedule helps teams order materials at the right time and keeps construction moving forward without interruption.
2) Preparing the Submittals Documents
Specialty contractors review project specs, performance requirements, and building codes for their work scope. Based on design specifications, teams gather relevant shop drawings, product data, and material samples. Each document must match contract requirements and meet applicable industry standards.
Contractors might submit documents individually or as complete packages. Single submittals, like concrete mix specs, often go through review first when early approval helps the project flow.
A complete package combines all related documents, from initial drawings to final product data, streamlining the review process for connected components. General contractors then review these submissions before sending them up the approval chain.
3) Reviewing the Construction Submittals
General contractors check each submittal against project contract specifications. A thorough review catches errors or discrepancies before documents reach the design team. GCs pay attention to how different specialty contractors' work connects, from scheduling to material compatibility.
Architects, engineers, and construction managers examine submittals after GC approval. Design teams verify that all components match their requirements and integrate properly with other building systems. Careful review prevents future change orders and scheduling conflicts between trades.
4) Responding to the Submittals
Design teams mark submittals with one of three responses: approved, approved with conditions, or rejected. Approved submittals allow contractors to start work immediately on their project sections.
Construction submittals marked "approved with conditions" need the design team to note specific changes. Contractors can begin work while addressing these corrections without resubmitting documents. Common conditions include minor material adjustments or small specification updates.
Rejected submittals require complete revision and resubmission. Rejections occur when materials differ from contract requirements or lack sufficient work scope details. Contractors must create new submittals addressing all rejection reasons before proceeding with work.
Project managers speed up approvals by matching submittals to contract specifications and design team requirements. Clear documentation and complete information reduce review cycles and prevent work delays.
5 Submittals and Submittal Approval Best Practices
Construction teams face numerous challenges with submittal creation and management - from tracking thousands of documents to preventing unauthorized installations.
Manual processes often lead to version control issues, delayed approvals, and communication breakdowns. Following these proven methods helps streamline the process while maintaining quality standards throughout projects.
1. Use Construction Document Management Software
Construction document management software stores submittal templates, logs, and schedules in one place.
Project managers using a platform built for construction like Access Coins can produce, distribute, search for and retrieve submittals and submittal packages.
Projects often contain thousands of submittal items spread across hundreds of specification pages, making digital organization essential for project efficiency.
2. Create Customized Reports
Construction project management software generates detailed status updates and performance metrics. Teams using software like Access Coins can track submittal progress, measuring efficiency at each approval stage.
Professional reporting tools let managers create branded PDF documents from submittal packages. Owners and stakeholders receive polished reports showing selected data in an organized format.
3. Centralize Submittal Markups
Multiple reviewers add notes, stamps, and changes to each submittal document. Manual processes across different platforms create confusion when teams mark up, rename, or reorder files.
Digital markup tools keep all annotations in one place. Project teams add text, highlights, shapes, and stamps directly within their ERP software, eliminating the need to switch between programs or re-upload files.
4. Keep Information Private and Secure
Modern software controls access to sensitive project data during submittal reviews. Project managers grant specific permissions to external partners through email-based systems, protecting confidential information.
Subcontractors and vendors submit or review documents without accessing the full project cloud database. Secure platforms maintain privacy while allowing smooth collaboration between all team members.
5. Implement Clear Submittal Statuses
Unapproved materials installed on projects risk removal at contractor expense. Clear status markers prevent costly mistakes and schedule delays from unauthorized installations.
Custom status indicators in project software match team terminology preferences. Project teams see approval status at a glance, reducing confusion about when to start construction phases.
Start Improving Your Submittal Process Today with Access Coins.
Effective submittal management stands at the core of successful construction projects. When teams streamline their documentation processes, they minimize costly rework, prevent delays, and maintain consistent quality standards. Modern solutions have transformed how construction teams handle submittals—from automated tracking to secure collaboration.
Access Coins ERP software makes managing construction submittals easier. Our platform helps teams track documents, automate approvals, and maintain security while providing the flexibility to adapt to your specific workflow needs.
Want to see how Access Coins streamlines your submittal process? Watch our 4-minute demo now to learn more about our construction management solutions, or book a personalized demo today and transform your submittal management.