What Is An Average Construction Company Profit Margin? & How To Increase Profit Margins In Construction
According to Turner and Townsend’s 2024 International Construction Market Survey, the average profit margin in the US construction industry is approximately 5%.
This impacts companies at every tier in the sector, with skyrocketing materials costs and rework leading to many construction companies struggling to turn a profit.
In this article, we look at the causes of low profit margins in the American construction industry, and what can be done to increase profit in the construction sector.
What Is The Average Construction Profit Margin In America?
The average construction profit margin in America in 2024 is 5%. A further breakdown of profit margins in the Turner and Townsend Construction Market Survey found the cities with the lowest construction profit margins in the USA are Houston, Austin and Atlanta at 3.5%. The highest is Nashville and Pheonix at 6%.
The report also revealed that 6 out of the 10 most expensive places to build in the world are in North America.
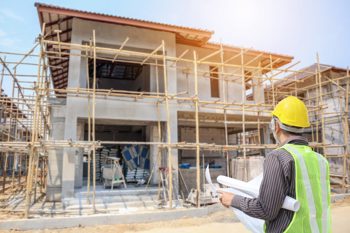
Why Are Construction Profit Margins So Low?
- Optimism Bias
- Insufficient Planning
- Poor Basic Data
- Risk Management
- Emergent Work and Rework
- Scope Creep
- Cost Increases (Labor, Equipment, and Materials)
- Changes In Legislation
Optimism Bias
Essentially, construction project managers need to be more realistic when it comes to deadlines and resources. The current significant workforce gap in the US construction industry tops over half a million missing workers, meaning skilled workers are in high demand. 2.7 times overbudget.
The effects of optimism bias in American construction projects is evident across the country, especially with large infrastructure projects. The MTA’s New York East Side Access project, which involved extending city lines to Long Island, finally completed in 2023, was delivered 14 years late and 2.7 times over its original budget.
Insufficient Planning
Planning and pre-construction is the most vital part of any construction project, and not spending enough time on cost estimating, procurement and scheduling will lead to blocks and delays later on in the project – which eats into profit.
Poor Basic Data
The construction industry is one of the least digitalized in the US. Where other industries embrace digital transformation, construction’s reliance on outdated tools such as Excel spreadsheets leads to poor data, poor communication and poor collaboration.
The result? Delays, overspend and a loss of profits.
Construction companies need to think long-term when it comes to generating profits, looking to solutions such as construction ERP to provide a consistent ‘single source of truth’.
Risk Management
Alongside the issue of optimism bias, the industry can also lack the foresight to assess projects for risks. While some risks, such as the COVID-19 crisis, simply cannot be predicted, others can be foreseen using high quality data and collaborative software to provide a vital ‘single source of truth’.
One of the advantages of the digitalization of the construction industry is technology’s power of spotting patterns and outliers, such as huge price increases, major availability gaps and inaccurate estimates.
Emergent Work and Rework
Rework is such a core issue in construction that an estimated $177 billion is spent every year on rework labor costs alone in the US construction sector. While some rework is simply unavoidable, much of it can be avoided through ensuring excellent collaboration in construction to avoid miscommunications, and once again spending more time on the pre-construction phase of a project.
Read more about How to Avoid Rework in Construction >
Scope Creep
Project managers in every industry are aware of the dangers of ‘scope creep’, where a client may push a project beyond its original parameters. With costs so high and profit so low in construction, scope creep can quickly translate to profit loss.
While scope creep can be unavoidable, as with risk assessment, it is worth investing in experienced construction project managers and finance leaders who can apply their experience to spotting and fighting scope creep at the beginning of a project. You can also use construction finance and accounting software to help you predict and manage scope creep.
Cost Increases (Labor, Equipment, and Materials)
A 2023 Gordian Report revealed that 82.5% of construction materials has experienced a significant cost increase since 2020, with an average increase of 19%.
Budgets have struggled to catch-up, with project overspend blighting more projects than ever since the economic shock of COVID-19. While recovery will come, it is vital for construction to take price shocks into account during the estimating and pre-construction stage to protect profits.
Labor prices have also increased in response to the construction skills gap, and need to be accounted for in the estimating and pre-construction phase.
While growth in construction costs across the nation have continued to ease from pandemic-charged highs, price levels will remain high for the foreseeable.
Read more about the Biggest Issues in the US Construction Industry >
Changes in Legislation
While legislation can move slowly, changes that happen in the middle of a project plan can impact on profits.
In July 2024, new California building codes come into effect which require large construction projects to embody carbon emission reduction, including using materials that meet specific emission limits. These legislation changes will impact a huge range of building projects, resulting in cost increases and delays.
Protect your Margins with the Leading ERP Built for Construction
Collaborate, control and connect with Access Coins - track all aspects of the construction lifecycle from a single source of truth. Book a demo with one of our construction technology experts.
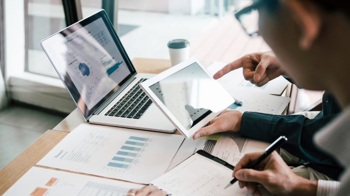
How To Increase Construction Profit Margins?
There are some key actions a construction business can do to help protect and boost profit margins.
- Avoid The ‘Race To The Bottom’ When Tendering
- Take Advantage of Digital Transformation
- Focus On People
- Build A Culture of Collaboration
Avoid The ‘Race To The Bottom’ When Tendering
The so-called ‘commoditization trap’ has led to a ‘race to the bottom’ culture in US construction, with contractors sending in the lowest price possible while not taking risks, price rises, rework and scope creep into consideration. While it is tempting to try and win projects with low prices, this results in rock-bottom profit margins and losses across the sector.
It helps to sell-in your specialisms, expertise and professionalism while tendering your projects – while you may not be putting in the lowest price, quality and good relationships count for a lot. It also pays to be picky with projects – if a project is making it clear they will go for the lowest price, then it is worth not investing the time and money into tendering and moving onto the next opportunity. This will lead to healthy profits in the long-term.
Take Advantage of Digital Transformation
The advantages of getting ahead in your construction digital transformation journey are countless. A construction ERP will help you with budgeting and forecasting to control costs, project management and your procurement process.
Having all of your data in a single connected system also helps with risk management, calculating costs, encourages collaboration and shares a single version of the truth within your team, avoiding the miscommunications which can lead to rework.
Technology also helps cut out hundreds of hours of manual administration work across a project through automation, leaving teams with more time to focus on vital growth-focused activity.
A new wave of technology, including cloud computing, AI, and big data are all useful tools for planning, productivity and profit.
Read more about the Benefits of using ERP in the Construction Industry >
Focus On People
In America, it is estimated that half a million skilled construction workers are needed to ease to construction labor crunch.
This means the staff in your business are some of the most vital resources you have.
Recruitment, training, and retainment can quickly cut into budgets on every level from the back office to on-site workers.
It is worth investing in health and safety training and focusing on building a positive culture within your company to ensure your most important asset remains with you and keep up the high productivity levels required in construction.
Build A Culture of Collaboration
Having a team on the same page and accessing the same information, especially in the planning and preconstruction phases of a job, will lead to a project running smoothly through to a successful and profitable endpoint.
Introducing consistent project management processes and having your entire team working on the same tools will help with the collaboration, which is vital for protecting your profit margins.
Building this culture can take time, but if you want to improve your profit margins in the long term, it is well worth investing time and money into giving your team the tools and expertise they need to work collaboratively.
Read our Buyer’s Guide to Construction Management Software >