Best Practices for Construction Data Management: Key takeaways, process, challenges & much more
Every stage of modern building projects generates huge amounts of data, from the first site survey to the last inspection. Construction companies also deal with a lot of paperwork, including design specifications, material procurement records, safety reports, and quality control reports. Good construction data management helps teams make informed decisions, comply with regulations, and finish projects on time.
This guide outlines at the essentials of construction data management and provides actionable strategies for implementing best practices in your organization.
Contents
- What is Construction Data?
- What is Construction Data Management?
- Data Management in Construction - Key Takeaways
- Why is Data Management Important in the Construction Industry?
- The Construction Data Management Process
- Challenges in Construction Data Management
- Best Practices for Construction Data Management
What is Construction Data?
A construction project's data includes design documents, financial records, material specifications, equipment logs, safety reports, and performance metrics. Information like this drives decision-making and ensures projects succeed.
General contractors and MEP (Mechanical, Electrical & Plumbing) contractors manage data across multiple departments and construction phases. Project managers track real-time progress metrics, while estimators use historical cost data. Finance teams process payments and track budgets, safety teams keep inspection records and incident reports, and field crews track their progress with digital tools and quality control logs.
Data like this guides not only current project execution but also long-term facility maintenance and future projects.
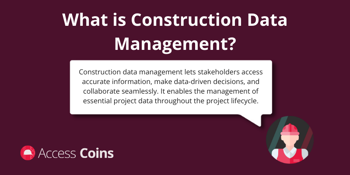
What is Construction Data Management?
Construction data management lets stakeholders access accurate information, make data-driven decisions, and collaborate seamlessly. It enables the management of essential project data throughout the project lifecycle.
Construction companies now choose digital solutions such a construction ERP system over paper documents and spreadsheets. Mobile field data collection apps and cloud-based construction management software connect field and office teams in real-time. BIM technology enhances project coordination and clash detection, while ERP systems streamline core business processes across organizations through automated reporting.
Data Management in Construction - Key Takeaways
- Organization - Project information flows from planning to completion, enabling teams to make informed decisions through digital solutions rather than paper-based processes.
- Core Elements - Quality control, cloud solutions, security practices, and well-defined governance standards form the foundation of successful construction data management.
- Key Challenges - Modern construction needs structured solutions to solve data quality, system integration, and security problems.
- Business Impact - Digital data management drives competitiveness through enhanced cooperation, cost control, and streamlined operations.
- Best Practices - Standardized data collection methodologies ensure consistency from initial site surveys through final inspections.
Get the Most from your Construction Data with Access Coins
Access Coins is an ERP platform built for construction that provides a single source of truth for all of your construction data.
Why is Data Management Important in the Construction Industry?
Data management in construction has transformed how teams work with project information, generating an estimated 2.5 quintillion bytes of data daily.
Project managers, superintendents, estimators, and field crews increasingly rely on accurate, accessible information to perform their roles effectively. Over 45% of construction companies use digital analytics tools, so strong data management practices deliver multiple benefits:
Strategic Planning and Analytics Implementation
Historic project data helps construction companies proactively transform their planning processes. With the construction data analytics market projected to grow to $10.8 billion, the industry is rapidly shifting toward data-driven decision-making.
Project managers analyze patterns from past projects to optimize timelines, allocate resources efficiently, and identify potential bottlenecks before they impact progress.
Integrated Resource and Supply Chain Management
Real-time tracking and analytics have changed resource allocation and supply chain operations. 68% of companies use advanced analytics. With these platforms, it's easy to track material counts, equipment maintenance, and even labor productivity.
Digital procurement platforms enhance supplier relationships through vendor rating systems, market intelligence tools, and automated purchase orders. It keeps inventory levels optimal, minimizes waste, and reduces idle time.
Risk Management and Compliance
Safety concerns, schedule delays, cost overruns, and quality issues are all potential risks.
Automated data collection systems streamline regulatory compliance through detailed records of safety protocols, environmental impact assessments, and quality control measures. An integrated approach helps companies maintain profitability while meeting complex regulatory requirements.
Quality Control and Site Operations
Advanced monitoring systems track construction progress and material quality in real time. Machine learning algorithms analyze safety incident patterns, while access control systems and wearable technology monitors personnel movement and vital signs.
This complete approach ensures consistent quality standards while maintaining optimal safety conditions.
Workforce Development and Knowledge Management
Data analytics transform workforce management through skills mapping tools, predictive staffing models, and personalized digital training platforms. Lessons-learned databases capture valuable project insights while knowledge-sharing platforms facilitate expert collaboration. Career progression and HR analytics help retain valuable employees through targeted development opportunities, and productivity analysis guides fair compensation programs.
Financial and Asset Optimization
Financial modeling gives you a lot of insight into project economics and asset usage. Cash flow forecasting prevents liquidity issues, and equipment maintenance scheduling cuts downtime. It keeps profit margins safe by guiding technology adoption and strategic planning. Construction accounting software can help you achieve this.
Client Relations and Market Intelligence
CRMs keep track of client preferences and project history. These systems keep track of industry trends, competitive positioning, and expansion opportunities. Using analytics to improve proposals increases win rates, while geographic information systems guide growth strategies.
Innovation and Technology Integration
Research and development tracking systems guide technology investment decisions through measured impact assessment and implementation analysis. Integration success metrics ensure seamless operation between systems, while competitive analysis tools track industry technology trends. Systematic innovation ensures continuous improvement while maximizing return on technology.
The Construction Data Management Process
Construction data management follows a systematic process from collection to security. Every step keeps project information accurate, accessible, and actionable.
Construction Data Collection
Teams gather information using digital forms, sensors, and IoT devices. The latest collection methods include digital forms for daily reports, IoT sensors, drones for site monitoring, BIM integration for design changes, and wearables for safety. Field teams collect critical data such as material quantities, labor hours, equipment usage, safety incidents, and quality inspections.
Construction Data Storage and Organization
Data management in the construction industry relies on cloud-based storage solutions organized by project phases and disciplines. Project folders follow a structured hierarchy:
- Contracts
- Drawings
- Specifications
- Submittals
- RFIs
- Change Orders
- Daily Reports
Using standard naming conventions ensures consistent file organization across all teams (e.g., "P100-SUB-MECH-001-R2" for mechanical submittal revisions).
Construction Data Validation
Systematic verification ensures the accuracy of information from property managers, architects, civil engineers, project managers, and logisticians. The process examines incoming data types, including text documents, images, PDFs, and CAD/BIM files, against predefined requirements and boundary values.
Quality control teams validate field measurements against design specifications while verifying material quantities and installation compliance. The results appear in summary tables, automated PDF reports, and interactive 3D models highlighting discrepancies. Automated notifications alert responsible team members to take timely corrective actions when validation reveals issues.
Construction Data Integration
Integration platforms connect core construction software systems. Data flows smoothly between project management, accounting, field reporting, scheduling, and document control systems. Integrated platforms automate document approvals, synchronize project data across departments, and reduce double entry.
MEP contractors benefit from specialized system integrations for coordinated design, procurement, and installation tracking.
Construction Data Analysis
Analytics turn raw data into actionable insights by:
- Performance tracking of labor productivity, equipment utilization, and material waste
- Predictive modeling for project delays, cost overruns, and resource bottlenecks
- Real-time dashboards showing project progress, earned value, and quality metrics
Construction Data Security and Governance
Security measures include role-based access controls that define what project data each team member can view or edit. Unlike subcontractors, client representatives have complete access to drawings and specifications—policies set up data backups, retention periods, and protocols for sharing sensitive information.
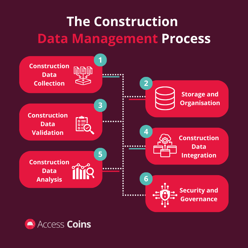
Challenges in Construction Data Management
Managing project data is challenging for construction companies, including general and MEP contractors. Understanding these obstacles is key to finding a good solution.
Bad or Incorrect Data
Manual data entry processes introduce significant risks of errors in construction project information. Teams relying on spreadsheets encounter persistent challenges with formula accuracy, version management, and data consistency. When multiple team members modify shared spreadsheets simultaneously, conflicting changes occur. Over time, complex formula structures become increasingly unreliable, affecting the integrity of project data.
Siloed or Fragmented Data
Disconnected software solutions create dangerous data gaps between departments. Project management, accounting, and field operations using separate systems trap critical information in silos. Fragmented data can delay decisions and lead to miscommunication and cost overruns.
Resistance to Change
Aging workforce demographics present significant challenges for technology adoption in construction. With an average age of 42.5 years and 22.3% of workers over 55, seasoned professionals often demonstrate skepticism toward new working methods. The disparity in technology adoption appears across construction sites, where older workers typically show more hesitation toward change compared to their younger counterparts.
About half of the global construction workforce will retire within the next decade, so these technological adaptation challenges are getting more pressing.
Security Vulnerabilities
Protecting internal operations and client data is important. Internal data includes pricing strategies and employee records, while client data covers building specifications and security systems. It's important to protect all vulnerable information from cyberattacks or data loss.
Collecting Noncompliant Data
Regulations and standards govern data management in construction. The California Consumer Privacy Act (CCPA) and other data protection laws apply to U.S. construction companies.
Noncompliance can lead to significant penalties. Team members need to keep state-specific privacy laws in mind when working on projects.
Best Practices for Construction Data Management
Construction companies can maximize their data value by implementing proven best practices. These practices make projects run smoothly and inform decisions. Following these guidelines improves project coordination and reduces errors.
Centralize your Data Under a 'Single Source of Truth'
Enterprise Resource Planning (ERP) software provides a unified platform for managing all construction data, from project plans to financial records. A centralized ERP system eliminates data inconsistencies and version control issues.
It synchronizes field operations with office management in real time, automates workflow processes, and standardizes department data. Businesses reduce errors and improve project coordination when all teams work from the same dataset.
Store your Data Securely in the Cloud
Modern cloud storage platforms offer significant advantages over traditional on-premises solutions. Subscription or license-based cloud systems eliminate hardware purchases and maintenance costs. Storage capacity easily scales with business needs through simple plan adjustments, avoiding the time-consuming hardware installations required by on-premises systems.based cloud systems eliminate hardware purchases and maintenance costs. Storage capacity easily scales with business needs through simple plan adjustments, avoiding the time-consuming hardware installations required by on-premises systems.
Cloud platforms protect your data through automated backups so you don't lose files or have a problem with your system. Teams can keep going no matter where they are with remote access. While reliable internet connectivity remains essential, many organizations find the flexibility and reduced infrastructure costs of cloud storage outweigh this consideration.
Develop Internal Data Management Protocols
Data handling protocols need to be clear. Data quality and security are everyone's responsibilities, from field workers to executives.
It's best to have documented entry and verification procedures, defined roles and responsibilities for data management, and regular security awareness training. Regular security audits also make it easy to comply with industry regulations and company standards.
Introduce Processes and Structures around Data Collection
Data collection in a standardized manner helps improve accuracy and consistency across all project phases. Businesses should implement structured procedures through the following:
- Custom digital forms that standardize data entry across teams
- Regular training sessions on proper data collection methods
- Data quality control procedures
- Regular audits to meet collection standards
- Guidelines for handling sensitive data
Maintaining data integrity and streamlining collection processes are key to these practices.
Streamline Your Construction Data Management with Access Coins
Good construction data management becomes more vital as projects become more complex and data volumes grow. Finding the right construction management solution means working with someone who can integrate your staff, systems, and operations.
Access Coins streamlines operations and improves data accuracy for construction companies, including dedicated support teams who understand how construction projects work.
Are you looking for a better way to manage your construction data? Contact us today to find out how we can help. Our team of digital transformation experts will help you every step of the way.